The construction industry is notoriously slow to change and productivity continues to decline. We see this firsthand, we read about it in trade publications and we talk about it at industry conferences. Embracing lean is one of the ways organizations choose to address this, but all too often they run into challenges that are difficult to overcome, which makes it so easy to revert back to their old standard way of operating.
With almost 15 years of experience helping organizations in the construction industry with various aspects of lean transformation, I’ve experienced successes and failures that may offer some help for other organizations on their lean journey. In this series of posts, I’ll go in depth on some of the key learnings I’ve had that often don’t get much air time. I don’t have all of the answers, but I do have a number of things I have stumbled into the hard way and had to experiment with others to figure out how to overcome!
Over this time, I’ve been involved in various discussions and debates searching for “the recipe” for lean transformation. Everyone seems to be looking for a silver bullet, or a copy/paste checklist for their transformation. While I don’t believe there is a one-size-fits-all answer, I do believe there are many common obstacles and challenges companies run into on their lean journey, and we ought to be learning from each other.
What does lean mean to you?
One challenge that frequently exists at the start of a lean journey is misalignment on a common understanding with the language being used, particularly around the word “lean.” One unfortunate thing about this is it can take months, years, or even decades for that issue to rise to the surface and be recognized. Niklas Modig did some great work articulating why the word “lean” is difficult for people to consistently understand.
The way Niklas describes this is that “lean” can be defined at many different levels of abstraction. “Lean” at a high level of abstraction is a philosophy, a set of values or a way of thinking. At a much lower level of abstraction, lean may be defined as a specific method or tool, like A3s. If we ask ten people to imagine “fruit” in their minds, you’ll likely get a variety of images. While they might all be “fruit”; a green apple, a rotten orange, purple seedless grapes, they are not all the same thing at all. It is much easier for people to consistently wrap their heads around a lower level of abstraction. If we ask those same ten people to imagine a “banana,” you will have much more consistent images.
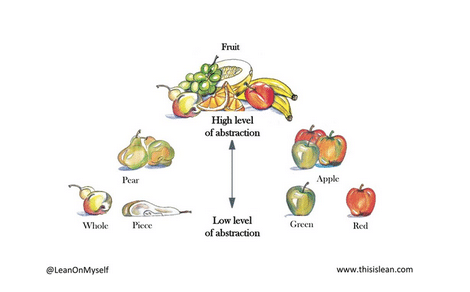
Illustration: Niklas Modig
When an organization begins an intentional start on their lean journey, they are often learning new things at a rapid pace and people feel like they are drinking from a firehose. Introductory training sessions are held at various levels and across the organizations and pilot projects are selected for Last Planner System®, Takt Construction or other process implementation. Employees throughout the organization begin to personalize their definition of “lean” based on their day-to-day experience, which varies from employee to employee. If employees are not involved with anything “lean” beyond their training, they begin to personalize their definition of “lean” based on what they see others doing from afar. This can create a big disparity in the understanding of lean or an oversimplification of lean. I know one very large construction company that initially thought to be lean simply meant all of their job trailers would have walls full of sticky notes!
Embracing lean at all levels is critical for a successful transformation
Many companies begin their lean journey without understanding that they are embarking on a journey. Instead they think they are simply implementing a tool or a process. Often, construction companies think that implementing the Last Planner System® on all of their projects will make them “lean.” Don’t get me wrong, implementing the Last Planner System on all of a company’s projects is a great goal to have, and it’s even better if you couple that with Takt Construction. After all, projects are the place where organizations in our industry are delivering the actual value to clients. However, in order for teams to fully optimize their flow and productivity, their organizations and support networks have to enable them. Things like getting materials, processing pay apps, getting trades paid, clunky construction software and many other things have to support the teams’ efforts to focus on flow. So, while starting with implementing LPS and Takt Construction across all projects is an excellent start, it’s important to realize to truly transform the company, you need to embrace lean at all levels of abstraction and throughout all aspects of the organization.
Miscommunication will hinder lean transformation
Why is misalignment of language a problem? If I think of “lean” as a philosophy and a way of managing, and I’m talking to someone who thinks of “lean” as doing Daily Huddles, we won’t be able to have a meaningful conversation about lean. We’ll expend time and effort trying to communicate, but we’ll both be misunderstanding each other which results in wasted time and a lack of alignment in the outcome of the conversation.
When you take into context all of the different people in an organization, all of the different specialties, and all of the ways to apply lean thinking, you can see there is a lot of room for misunderstanding and miscommunication that can get in the way of an organization’s momentum in a transformation of any kind.
Are you talking about apples or oranges?
What’s one to do about this? For starters, just recognize that when two people say “lean” there is a good chance they are talking about apples and oranges. Recognition of this can is the first step that leads to a different, better, conversation. Before I recognized this was a problem, I would always start my efforts with organizations with a standard, high abstraction, definition of lean. Sometimes I would start with one the organization was already using, other times I brought one to them. Generally, this starting definition would talk about “lean” as a philosophy and a never-ending journey based on continuous improvement and respect for people. This was helpful to some extent, but what I didn’t yet realize was people were still understanding it differently. I had yet to learn that high level abstractions are difficult to create alignment around.
Once I stumbled into Niklas’s analogy with the fruit and I realized the need for more distinction, things got much better. I had a graphic similar to the fruit graphic created, but we made it directly relevant to the organization I was working with. This graphic and conversation became part of all of our standard training going forward. This way it was in the forefront of people’s brains as they began to learn about something new and they understood where those things fell in the order of abstractions. This may seem simple, but the impact from it has been exponential. If you don’t already have something similar, creating a similar framework would be a great step to take on in your organization, even if your company’s been on your journey for years.
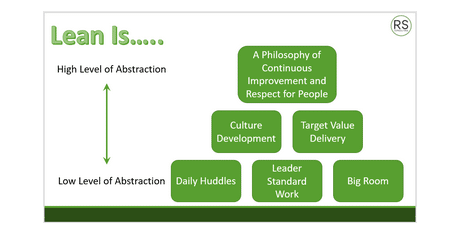
Continuous improvement to my approach
Now I’m testing out a slightly new approach. Recently I’ve been working with an organization that does not have a common definition of lean. Rather than provide them with a definition, I spent time with some executives in a room together to define together what “lean” means to them individually so we could create the high-level abstraction together. By doing this with them, they’ll have a better (and a common) understanding amongst themselves. As the team advances in their engagement with lean, we’ll formalize a high abstraction definition together. After that we can begin to define the mid and lower abstractions that are most relevant to their organization together.
Have you seen this issue in your organization? What other things have you done to overcome this and to bring peoples’ understandings into alignment? What else can we try?
Stay tuned for my next article on lessons learned with lean transformation.
Feature image: Regine Tholen via Unsplash.
Related articles
How to Empower Lean Project Teams for Success
Confessions of a Social Researcher in the Building Industry
Rebecca Snelling, owner of RS Consulting, coaches people, teams and organizations on leadership and Lean Transformation with an emphasis on advancing culture. She started in the construction industry in 1996 and began coaching companies and teams in 2006 with a focus on applying Lean principles in various organizations and project types. She works with owners, architects, contractors, engineers and trade partners, as well as full project delivery teams. She coaches leaders at all levels to integrate lean thinking into their organization and develops Lean Coaches to effectively facilitate, train and coach others implementing lean practices and behaviors.
She has been actively involved in the Lean Construction Institute (LCI) since 2008 and is a contributing author of both LCI books: Transforming Design and Construction, a Framework for Change, and Target Value Delivery: Practitioner Guidebook to Implementation. Rebecca is the Chair of the LCI Board of Directors and sits on the Board for the Center for Innovation in the Design and Construction Industry (CIDCI).