How to Empower Your Lean Project Team for Success (Part 1)
Sharing is Caring
Imagine you are planning a vacation in Italy in a few months. Do you go to a travel agent to have your trip mapped out meticulously beforehand? Do you plan every step of your time abroad? Do you like to know precisely what you are going to do at any time of your trip?
Or, are you the type of person who slings a bag over your shoulder, hops a plane and takes Italy one espresso, pasta dish and glass of Amarone at a time? In preparation, did you read books, watch shows, seek advice from every waiter/college student/past visitor/current citizen of Italy to create a mental list of things to do in your head? Are you mulling things over for a while before you decide what to do and see?
It doesn't take much to imagine these two people meeting each other on a project team. They don't know each other well. They don't know what makes the other person tick, what motivates them, how they assess risks and concerns, or how they make decisions.
This happens all the time in the construction industry, and it breeds misunderstandings, wrong assumptions, and a lack of trust, which ultimately will result in poor project outcomes.
Collaboration right from the start is crucial for success
Construction projects involve multiple companies with multiple people in these companies that often have little experience working together. I have spent a lot of time working with project teams over the past 20 years and what I have noticed is we do very little to overcome that reality.
Our challenge is to make them collaborate and perform as a team at a high level, very quickly right from the start. This collaboration includes having tough conversations around budget, design, scheduling, and all the elements that make a project successful.
Lack of trust equals project failure
Often, people come to these projects with their traditional mindset of competing agendas, competing budgets, and competing objectives. They tend to fight for their own because they have to work with people they don’t know and they don’t trust. As a result, people make decisions based on assumptions rather than conversations to clarify the different perspectives, the knowledge of the group, expectations of each party, the actual facts, and possibly their individual goals.
Very early on, this lack of trust sets the course for project failure, or at a minimum unrealized potential.
To make Lean projects successful, we need to onboard team members to explain and then show them what is different this time. In other words, we need to do a better job training them with behavior and leadership skills that are critical to making the process and project successful.
What if you don’t have the luxury of time?
Now, the tricky thing with behavior change is that you can't just tell someone to behave differently if this new behavior is contrary to their beliefs and values or to believe something else if it is different from what experience has shown them. That is the culture of the individual, the team, or the company. Such an imposed change won't be sustainable.
To shift this culture with sustainability and impact, we need to give people new experiences, which is a process that can take years. There is evidence that project teams who have been working together for years start creating a new norm and team culture. And if new people join the team, it is easy to integrate them into the new culture.
Unfortunately, construction projects don't have the luxury of that time frame. The integration of all team members needs to happen as quickly as possible at the beginning of the project, and ongoing as the players come and go through the course of the design and construction phases. Additionally, add in that there never seems to be enough time to create the space for team development when the team is under the gun to get into permit, meet budget goals and remain on schedule.
Similar to an organizational culture, to create a successful project team culture, your project strategy needs to have a concurrent leadership strategy. The solution we have come up with is to create opportunities for the team members to share experiences that enable a team binding culture and help shift their mindset quickly. Taking the time to do this early pays dividends over the course of the project and like many aspects of Lean Thinking you need to go slow to go fast. Focus on the foundation of your team and not just your building.

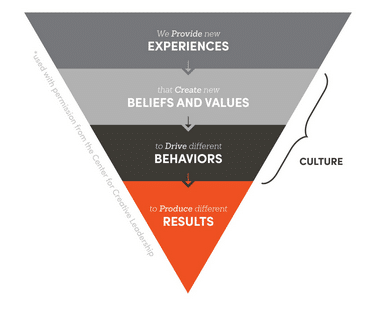
Is your team (dys)functioning?
To better understand how teams work, I recommend reading The Five Dysfunctions of a Team by Patrick Lencioni. In his book, the author tells the story of a technology company that is struggling to find customers and to grow because the leadership team does not show up as a team and thus affects the entire organization in a negative way. This is even more common when the leadership of a construction project team is leading multiple players from multiple companies, or on a Lean Project Team where the leadership is from across multiple companies.
Patrick Lencioni differentiates the following five dysfunctions of a team:
- Absence of trust
- Fear of conflict
- Lack of commitment
- Avoidance of accountability and
- Inattention to results.
The role of the leadership team is to overcome these dysfunctions by being a role model for the team, by being authentic, vulnerable, encouraging creativity and diversity, debates, and different approaches to solving a problem. Team leaders also need to communicate deadlines, goals, and project outcomes clearly.
What Patrick Lencioni found is that
“Successful teamwork is not about mastering subtle, sophisticated theories, but rather about combining common sense with uncommon levels of discipline and persistence. Ironically, teams succeed because they are exceedingly human. By acknowledging the imperfections of their humanity, members of functional teams overcome the natural tendencies that make teamwork so elusive.”
Sharing is caring
A great icebreaker exercise, suggested by Patrick Lencioni, to build rapport, connection, and interaction on a human level is to get the team members together and have them answer the following questions:
- Where were you born?
- Where are you in the family?
- What is your proudest achievement?
- What is your hobby?
By having them share their answers, their unconscious mind starts creating new connections and rapport with the other team members. They find common interests and discover that nobody is perfect. They interact on a human level.
Conclusion
Since we started embracing our team members’ humanity and imperfections and recognizing each other for who they are and the uniqueness they contribute, we are finding that the collaboration on our projects and within our teams becomes much easier, faster, and results in more successful outcomes. A healthy culture, where team members see each other as peers and respect each other, on all projects and especially Lean Projects, is the foundation for the most successful outcomes. Read more on this topic in our article Leveraging CoLocation and Lean Principles for Design Success.
No matter what personality types you have on your project team, seek to understand and embrace their diversity and encourage connections on a human level.
And remember: there are many roads that lead to Rome!
Jessica Kelley has more than 20 years of experience integrating Lean thinking on projects across large organizations in the construction industry to achieve cultural transformation. As the Operational Excellence Manager at Southland Industries, she is responsible for the design and implementation of lean business systems resulting in high levels of employee engagement, customer satisfaction, process improvement, and financial benefits. She also manages the operational excellence road map and is a mentor, facilitator, trainer, and coach for the company’s employees. She is a member of the Lean Construction Institute, the Project Production Systems Laboratory at UC Berkeley, the Center for Innovation in the Design and Construction Industry, and the Construction Industry Resource Training Network.