As the Founder of Inertia Systems, my focus is on the development of intelligent construction documents to help diverse project teams retrieve critical information onsite, on their mobile devices, to make informed decisions in the field.
In my previous article What Project Owners Should Know About Intelligent Construction Drawings, I explained how intelligent construction documents can eliminate non-value-adding steps, aka waste, on construction projects.
In this article, I share my thoughts on the future of construction. The central question is how construction teams can leverage the best technology to manage all the things they can control and to avoid all the avoidable things.
Avoid what is avoidable
If you unwind and unwrap the process of construction workflow, it is highly inefficient due to numerous steps that we can avoid. And if you eliminate these steps, you will achieve true optimization. Of course, there are things you cannot avoid, for example, supply chain issues, wars around the world, traffic on the freeway, and many more. Events are going to happen that we can't control.
Some things will remain uncertain. Uncertainty is one of the biggest issues people try to plan for. They aim to decrease the risks that come with certain events. It is the same on construction sites, where risk management plays an important role in the success of a project.
One of the simplest things you can do, instead of trying to control the things you can't control, is to use technologies, processes, teams, and contracts that support risk management.
How can intelligent technology help?
The central idea is to make information more rapidly accessible, like the concepts of search engines or Chat GPT; to leverage technology to make important information accessible when you need it. Knowing where information is stored or archived is not enough. Because if you can’t retrieve critical information when you need it, why would you store it in the first place?
Technology can help solve this dilemma. There's software technology, and there's hardware technology. You can swing the hammer or you can use a nail gun if you want to get a nail in the wall. What’s the better solution? What’s more efficient?
If the outcome you're after is building a wall correctly, the data is going to help you improve the process. Data will help you have all the team members where they are supposed to be, on time, on schedule, and with the information they need to do their job correctly right from the start.
Intelligent software technology can help teams collaborate, stay informed, and have access to real-time information, real-time statuses, and real-time changes.
What type of software do you need?
There are powerful software tools available, but because they are complicated to learn and use, the masses don’t utilize them. On the other hand, there are some really simple software tools out there, but they are too simple and don't solve enough problems, capture enough data, or communicate enough information. Which means they don’t generate any value.
Generally speaking, there are two types of software:
- Software that automates, and
- Software that allows humans to do tasks manually and accurately.
The first type is automation software that creates reality footage and generates respective reports. An example is drones that capture progress in daily, weekly, or monthly intervals.
The second type of software is what we do at Inertia. The idea is that software technology can capture real-time statuses or changes in meaningful ways for the team.
This is critical for construction teams, which typically involve numerous stakeholders (owners, general contractors, subcontractors, jurisdiction, and many others). All of those people need to be on the same page about the project's progress. They need to be able to do the right thing at the right time.
So how do they know what the right thing is?
Usually, there is a schedule and one tool that states where and when everyone needs to be. Then, there is a status tracker and a cost tracker. If these tools do not communicate with each other, payments don’t get released, which means that products do not get ordered, which will slow down the entire workflow and create waste.
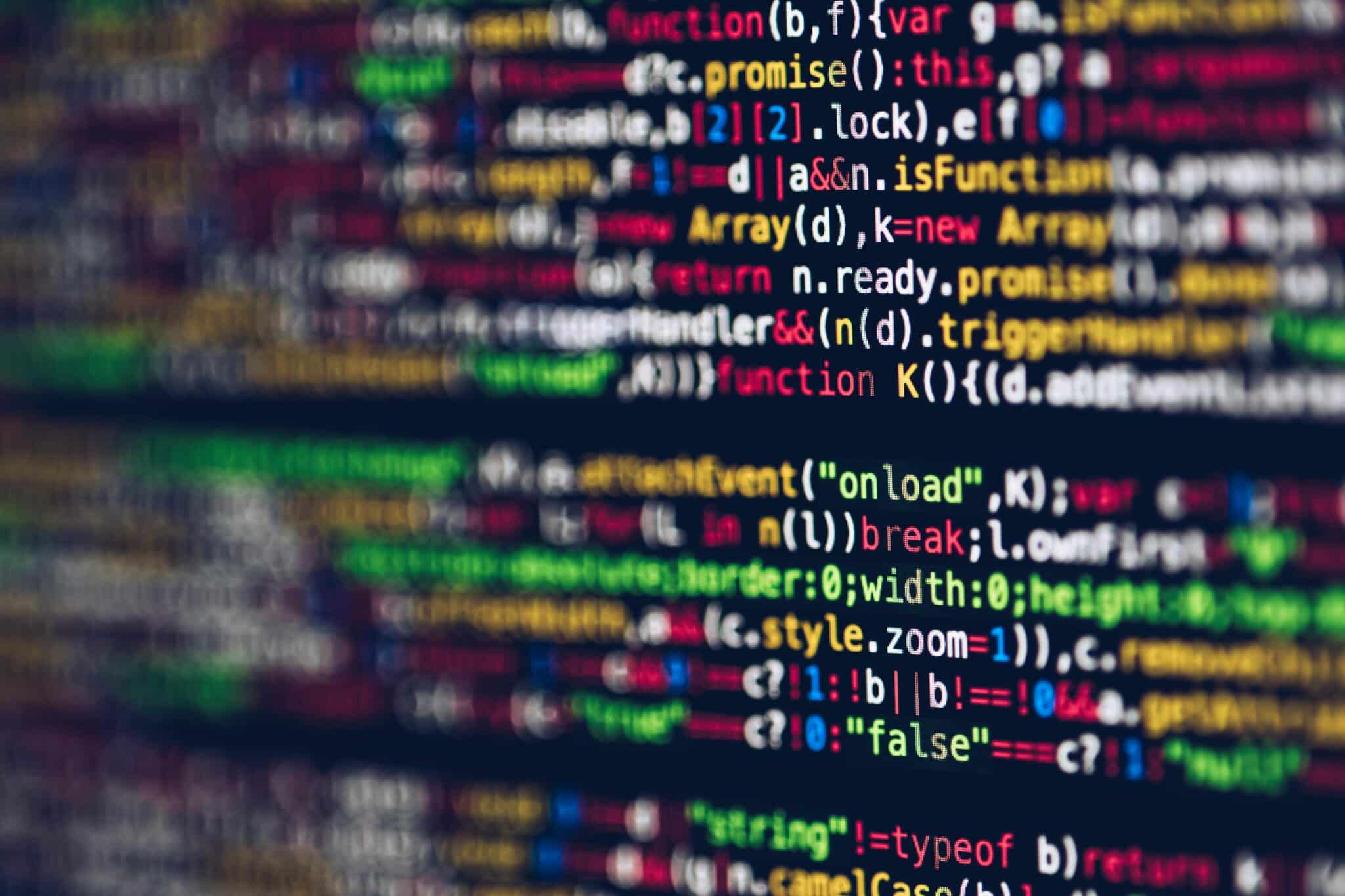
Image: Markus Spiske via Pexels
Good software will sync disconnected data
Good software technology will sync all that disconnected siloed data in a way that everyone stays informed with real-time status, with all the different things that have to happen amongst all the different stakeholders.
In other words, technology connects teams better and allows them to collaborate more efficiently. It organizes the data in the best way possible to make it accessible when team members need it. Additionally, technology needs to be easy to use.
What does integration mean?
A lot of people talk about integration because it has become a buzzword. What does it mean?
To fully maximize integration, speed to value and the end result is what matters. This means that integration is only valuable if it tells you the status that is going to impact your success or failure on your next task.
If all you get is information spread across different folders, which you have to search for to make matters worse, you are not capitalizing on the advantages of true integration.
Intelligent software can connect all the disconnected data. It organizes your data in a structured way, it can standardize how people capture and, more importantly, access data in real time to better perform their tasks.
Technology and human labor need to integrate
Additionally, robotics and 3D printing will disrupt the construction industry. There will be virtual and augmented reality and many futuristic concepts. However, the majority of construction projects will still rely on a lot of human labor, on connecting a lot of physical products that people deliver to a certain place and point in time, and all these processes need to be coordinated in an efficient way to maximize profitability.
In the coming years, construction teams will use more and more technology in all those different areas to make their projects as efficient, profitable, and valuable as possible.
The hurdle of change resistance
Our true competition is the status quo. Projects and people in construction are change adverse. They've always done it a certain way, which means the outcome is predictable. They know they are getting two per cent profit with their way of doing things.
Whereas we can offer them six per cent if they avoid specific mistakes. But because this is a new approach that requires learning, change, and a behavioral shift and bears the risk of the unknown, they rather stay in their comfort zone even if this means they are not getting better results.
Overcoming Resistance to Change
New software should be easy to adopt and integrate seamlessly
Another reason why people do not adopt new software technology is the flood of software on the market, which is overwhelming for a lot of people.
Project managers who focus on getting their projects built don’t want to invest in learning new software. Their issue is that they don’t know whether a new software will deliver what it promises and whether it is a wise investment in the long haul because you can’t prove it in a week or months; it can take years.
How can a project manager sample 100 software solutions? Do you have to wait for 100 projects, or do you try multiple at a time? Evaluation is very tricky because of the nature of the construction industry.
As a software supplier, we have to break through this noise and demonstrate speed to value without being too disruptive. Project teams need to feel that a new software solution is easy to adopt and integrates seamlessly into their status quo while, at the same time, delivering incremental value. A lot of software is not achieving these requirements, and the future of construction lies in intelligent technology that can do all those things.
3D printing and robotics will disrupt the industry
What’s unique about the construction industry is that you have to go where the work is. This means all the products and technology you need for the project need to be onsite. If you use 3D printing and robotics to do certain tasks onsite, the 3D printer and robot have to be delivered there. And every job site is unique, which means it has its own variables to navigate, the technology may need to be set up differently, which may present different challenges. There is no one-size-fits-all solution in construction.
And this is where the intersection with the human skill set takes place. The challenge is to find people who know how to adapt to all these variables in the unique job environment and still get the job done.
As a project manager, this will be one of your checkboxes.
How do I factor into all the unique variables on one particular project and make it work?
Which technology can I use to accelerate and improve my project and margins?
As soon as new (software) technology proves a return on investment and improves compatibility, more projects will start adopting it.
Things you can control will be improved by using robots that have proven efficiency and accuracy. Automated data capture tools can deliver added value eventually. The key thing here is the connection of people and technology in a meaningful way and delivering the critical data when and where it is needed in real time.
Lessons learned are critically important
Referring to lean principles, lessons learned are a key point. What did we learn on this project? What did we do right? What did we do wrong? How can we do better next time?
Unless you can capture the lessons learned in detail, not just like a theory or a concept, you won’t improve. Inertia software can provide this capacity. Because everything is organized in objects, every problem and solution referring to a specific object is retrievable for future project teams who deal with a similar product. Previous mistakes will not happen again because the software immediately alerts the team that there was a problem with this specific object and how it got solved.
Taking Advantage of IPD Lessons Learned
You don’t know what you don’t know
People don’t know what they don’t know. This also applies to the construction industry.
For a project manager, it is easy to plan for all the things he knows. And there are great tools to do this.
But then there are all the things that he doesn't know. They are going to happen, but he doesn't know what they are and when they are going to come up.
So the better you can manage those unknown things, the better you are prepared for uncertainty, and the more successful your construction project will be.
The solution will be intelligent tools and technology that help you manage those unknown events effectively and mitigate the risk from these unknown scenarios.
Feature image: thisisengineering via Pexels
Matthew Hudelson is the Founder of Inertia Systems. Since 2010, he has worked alongside builders, owners, inspectors, architects, and other project team members to learn how Inertia tools and workflows impact the challenges on construction sites. In turn, Inertia provides intelligent construction software to eliminate waste and improve efficiency throughout every step of the construction process.
No matter how large the team, Inertia’s intelligent construction drawing software delivers visually connected information, automatic updates and notifications, which helps reduce waste on construction sites, and improves construction workflow, and project outcomes.
Clients include the Parnassus Hospital, UCSF Medical Center, the SoFi Stadium, and Stanford University.