Construction Productivity in the United States has been declining for the last 50 years.
Research by Paul Teichotz from Stanford Univerity & CIFE compares construction productivity to other Non-Farm Productivity in the United States since 1964. While most industries have more than doubled their productivity, construction has actually decreased.
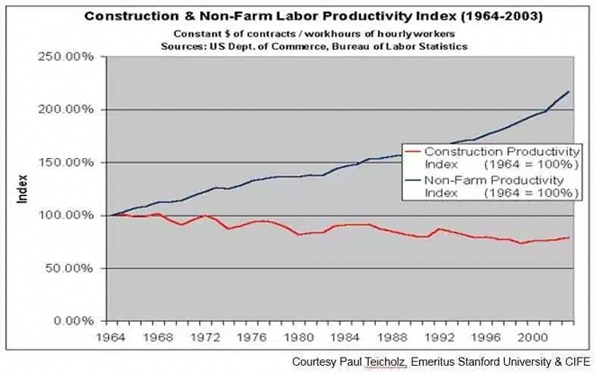
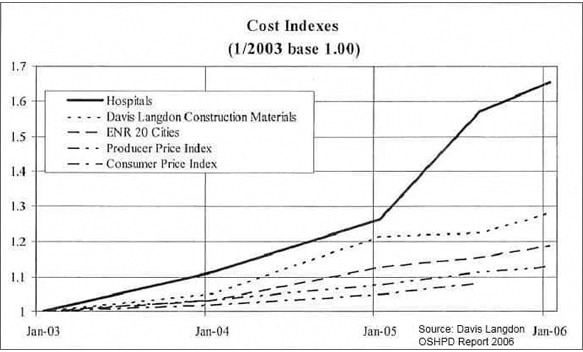
Aren't we pretty good at this?
Research from Davis-Langdon prepared in 2006 shows costs of hospital construction in California escalating significantly faster than other construction types.
Wasted Time in Construction is Out of Control.
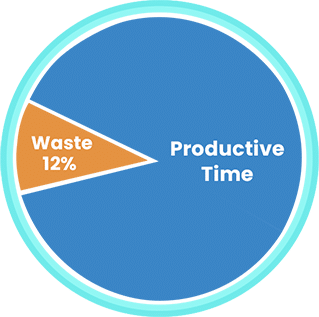
The Construction Industry Institute (CII) published a report in 2004 comparing wasted time vs productive time in the manufacturing and the construction industry.
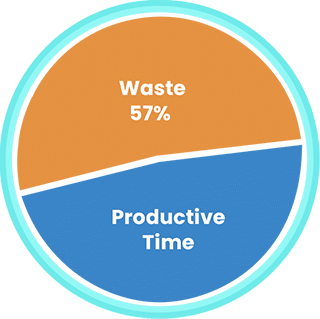
88% of time in manufacturing was found to be productive (value added) vs only 43 % of time spent in construction. This reports demonstrates that more than 50% of time spent on construction sites is waste (non value added).
What is Manufacturing Doing Differently?
What do the best manufacturers do that the design and construction industry can learn?
Toyota is recognized as one of the world's most efficient and well run manufacturing businesses.
In his book The Toyota Way, Jeffrey Liker lays out of the foundation of Toyota's operating system. Many of these components and principles are now known in summary as Lean.
14 Management Principles based around Continuous Improvement and Respect for People.
Focus on 8 Wastes: Identify them then reduce and/or eliminate.
-
Defects
-
Over Production
-
Waiting
-
Over Processing
-
Transportation
-
Inventory
-
Motion
-
Unused Employee Creativity
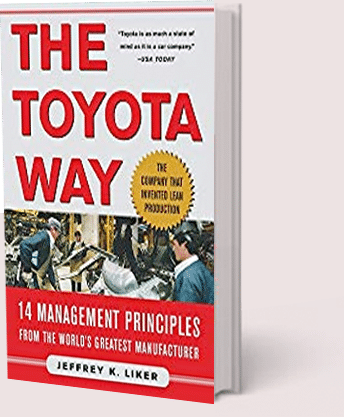
A Different Team Structure
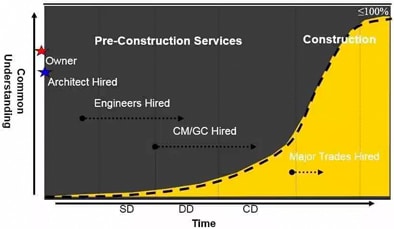
Traditional Silos separate Customer Value, Design of a System and its Construction; creating inefficiencies and waste within the project delivery chain.
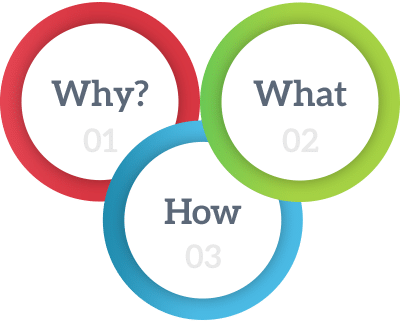
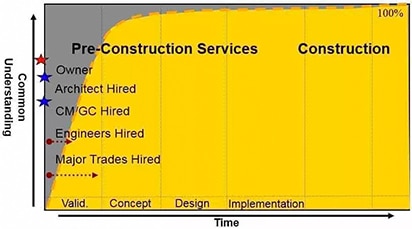
Lean Construction looks to break down traditional silos and couple the why, what and how of project delivery into an integrated system that flows from start to finish.
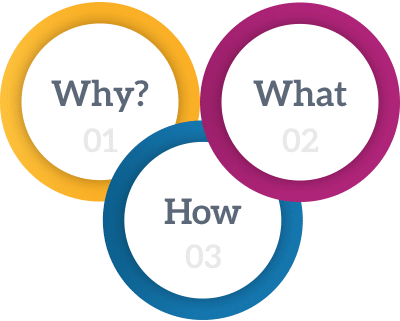
Lean Construction seeks to organize teams in ways to facilitate and drive collaborative communication.
By allowing the right people to talk to each other at the right times without tightly controlling the communication flow, projects can move quickly, make better decisions and eliminate inefficiency caused by latency.
Integrated Project Delivery takes this a step further by contracting for the entire design and construction team under a single contract with the owner and centering decision making authority within a Core Group made up of design, construction and owner representatives.
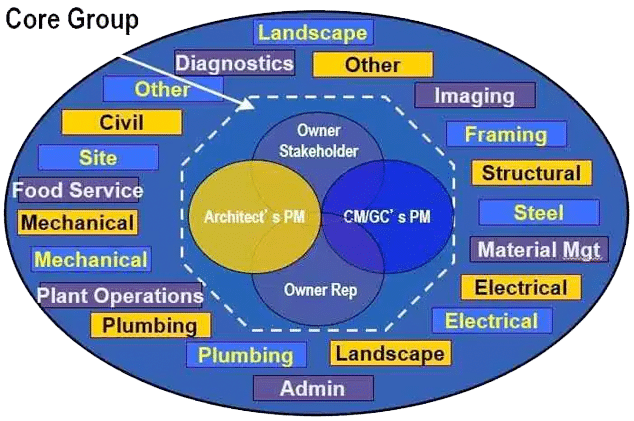
New Work Processes
Last Planner System
Based on research done by the Construction Industry Institute (CII) in the early 1990's, typical projects which are considered successful have a one week planning reliability of only 54%. This means that work planned to be complete on a specific day on the following week will be done on that day just slightly better than the odds of a coin toss.
With this 54% compounding each week over the life of a project, no plan survives even one month of traditional project delivery without needing a complete overhaul.
Glenn Ballard and Greg Howell developed the Last Planner System as a means of driving reliability into the planning and execution process for construction projects.
The Last Planner System consists of 5 connected conversations:
- Milestone Planning
- Phase "Pull" Planning
- Mark Ready Planning
- Weekly Work Planning
- Learning (Percent Planned Complete and Variance Tracking)
To see how Last Planner is applied on a specific project
Click Here
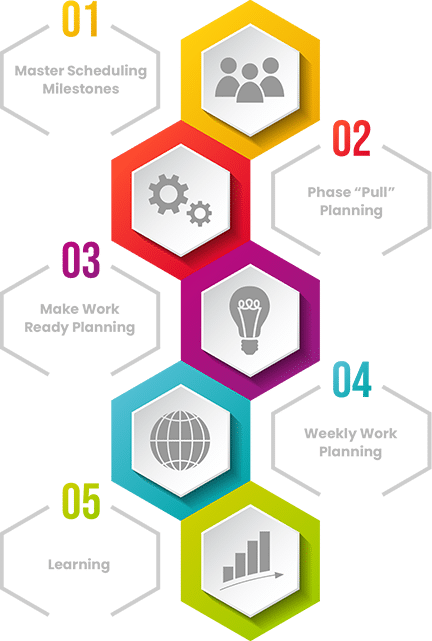
Last Planner System
Projects using Lean concepts focus on reliable promising to increase reliability of hand offs. Think of passing a baton in a relay race.
Reliable promises consist of 4 steps:
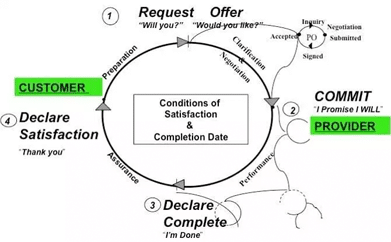
-
01
A Request is Made.
-
02
A Promisor Makes a Commitment.
-
03
The Promisor Declares the Commitment Complete.
-
04
The Requestor Confirms the Commitment is Complete.
Last Planner System
Traditionally, teams look to make decisions about options before proceeding into the detailing of those systems. Set Based Design is a concept of advancing multiple designs in order to make the best decision based on additional information.
Instead of picking a structural system for a new building prior to detailing it, a project might advance three separate systems into the Design Development phase of a project along with floor plans and shaft layout. By continuing to advance multiple sets, the team can make a decision later with significantly more information.
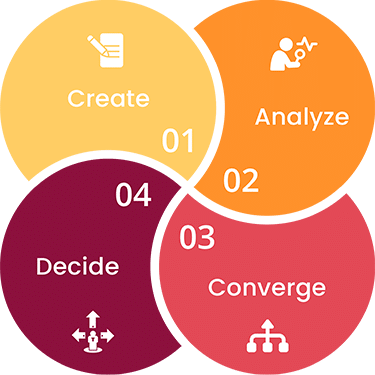
A3 Problem Solving
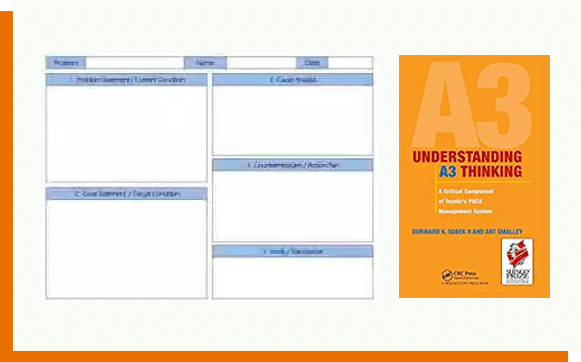
An A3 is a structured process of documenting a problem, options, proposed solution and action plan on a single sheet of paper. A3 references the standard 11"x 17" sheet of paper.
Developing an A3 is done collaboratively with all stakeholders. The process helps to generate consensus around the proposed path forward by first gaining consensus around the problem statement.
By summarizing all of the information on a single sheet of paper, the decision and action is distilled down to its most important elements. A rule of thumb - it shouldn't take more than 5 minutes to present all of the information on an A3 to decision makers and approvers.
Choosing By Advantages
Choosing by Advantages (CBA) is a systematic decision making process developed by Jim Suhr which focuses on advantages of options. While most systems focus on pros and cons, CBA removes cons by recognizing that a con can also be expressed as an advantage for one or more of the other options.
Advantages are weighed in importance against each other with the most important or "paramount" advantage having the most weight. CBA works well to gain consensus with a large group of people with differing goals and values.
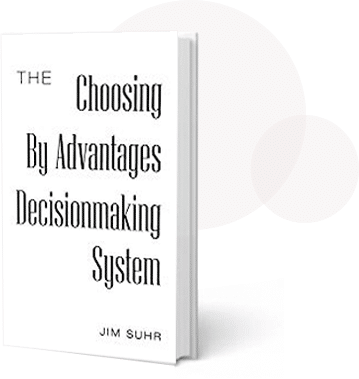
Choosing By Advantages
High performing teams and projects maintain a commitment to continuous improvement. One way to drive positive change is to implement a plus/delta at the end of each meeting and event.
A facilitator takes 5 minutes or less to capture Plus / Deltas.
Plus: Something that went well and should be repeated. Delta: Something that didn't go well and should be changed or altered next time.
Teams assign each delta to a specific individual with an action plan and commitment for completion. With a commitment to identifying and adjusting deltas, processes will improve over the life of a project or team and lead to outstanding results.
Sample Plus/Delta after a meeting
Lean Construction Institute
Founded in 1997, Lean Construction Institute (LCI) seeks to improve the Construction and Design industries through Lean approaches to project design and delivery. LCI’s member base is comprised of owners, the design community (architect and engineering firms), general contractors and trade contractors.
Lean Construction Institute is the recognized leader in providing information, training and research to the design and construction industry with a goal of transforming the built environment.
Their website is a valuable resource for all levels from beginner to advanced practitioners.
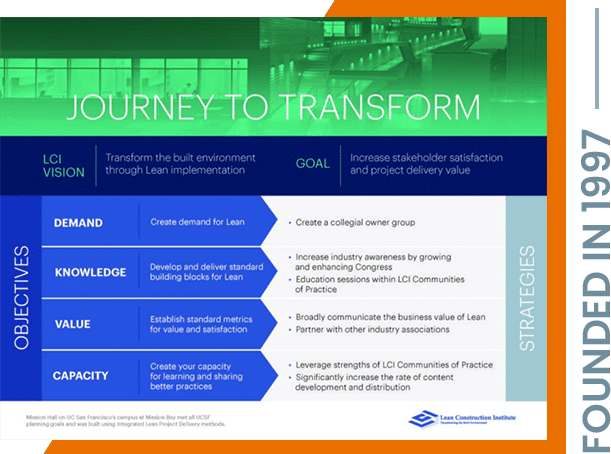
Something to Think About. . .
Data suggests that projects implementing Lean concepts and tools are more likely to finish on budget and a head of schedule.
In order to improve efficiency, we must first learn to identify inefficiency or waste in systems. Research done by McGraw Hill in 2013 shows that just by learning about Lean concepts, people begin to see the construction industry as highly inefficient. Those without an understanding of Lean see the construction industry as highly efficient.
Improvement is not possible without a recognition of the waste in current processes and methods.
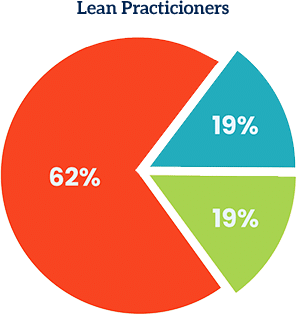
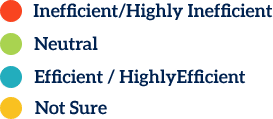
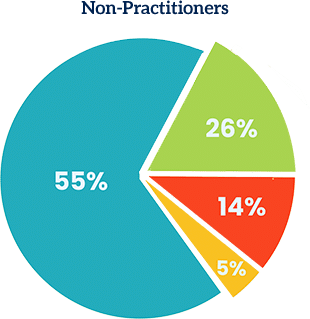
Perceived Efficiency of Construction Processes in the Industry
(by level of Lean Engagement)
McGraw Hill 2013