How is IPD Different From Other Contracting Models?
Integrated Project Delivery sets up a different environment than other delivery models such as lump sum, design/build, and guaranteed maximum price contracts.
An area where this is most evident is in how field coordination and errors/omissions type issues are treated contractually.
This page examines a case study where a complex issue was identified and how it was resolved by an IPD team.
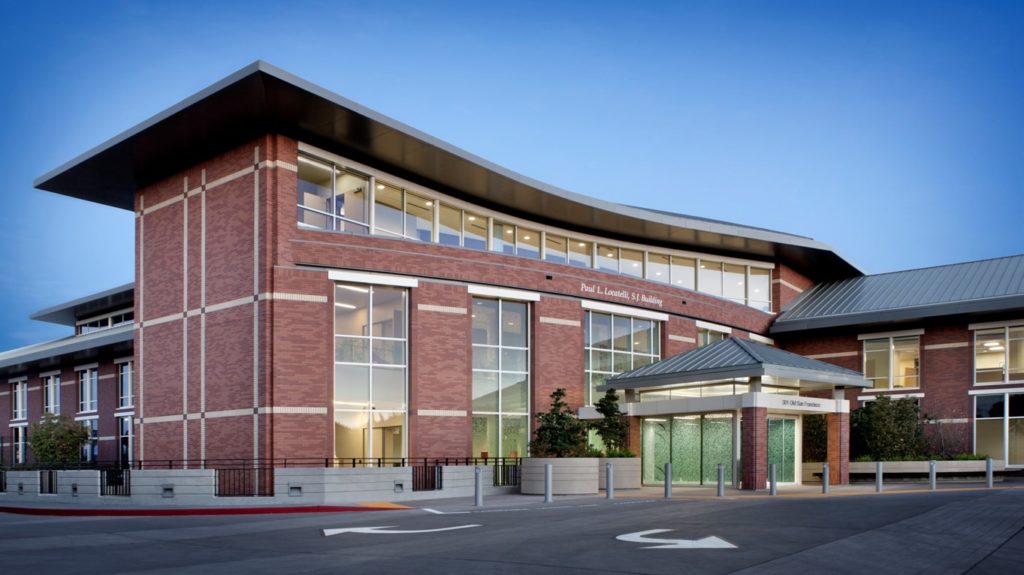
Background and Construction Summary
This ground up medical office building has a standing seam metal roof that cantilevers up to 8 feet past the exterior wall of the building. The underside of the soffit this creates is finished with metal panels. The exterior wall of the building is made with individual thin bricks placed on a water proofing membrane.
In order to get the shape of the roof and the cantelever, the team elected to use prefabricated light gauge metal trusses. The structural engineer (a risk/reward partner) provided the expected loading criteria to the team. The exterior skin trade partner (a risk/reward partner), bid the truss scope with the design criteria to a lump sum design/build truss contractor (not a risk/reward partner).
There were over 1000 trusses supplied and installed on the project. Many of them were unique due to the contour of the building footprint and unique conditions.
Construction Sequencing
- Each individual truss is placed on top of the concrete roof deck and attached in place.
- The trusses have cribbing installed between then for lateral bracing after installation in the field .
- Two rows of sprinklers are placed within the rows of trusses.
- Dense glass, then a water proofing membrane and finally the standing seem roof is placed over the trusses.
- The metal panels are placed on the underside of the soffit formed by the trusses.
- The brick is brought up the vertical face of the building and overlaps the metal panels on the soffit.
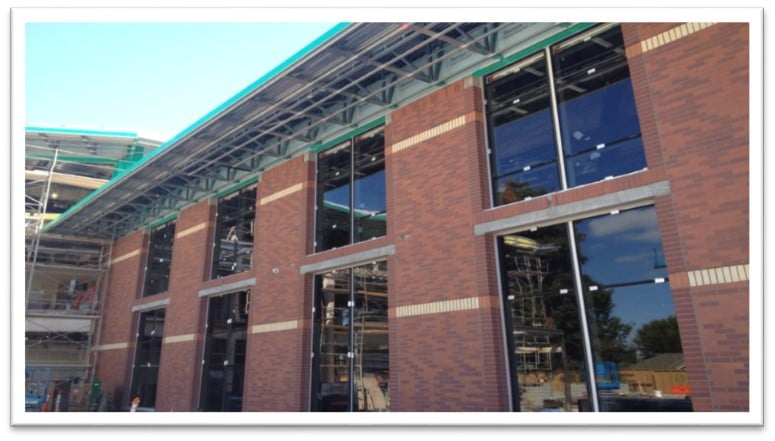
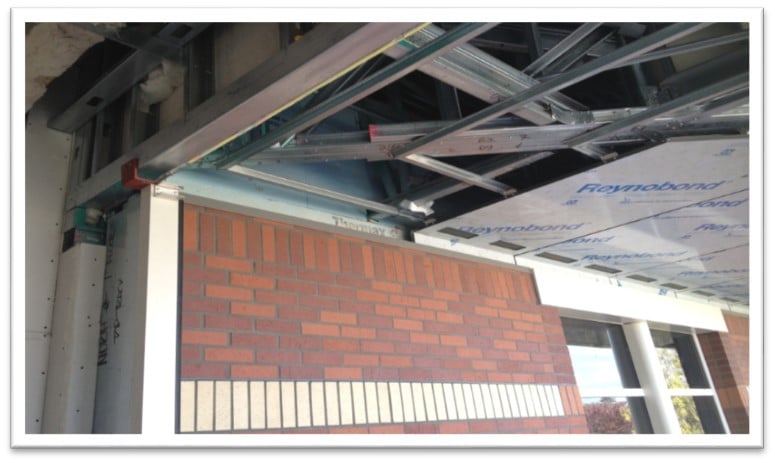
Construction Sequencing
The angle of the metal panels on the underside of the soffit to the brick on the vertical face needs to be 90 degrees. In this case, it was less than 90 degrees, meaning that the soffit was not perfectly flat; it was actually "sagging" as it projected out from the edge of the building.
It was eventually determined that the trusses were sagging 3 times the maximum allowed deflection. This was considered a major construction issue by the the team and an investigation ensued to determine the root cause.
Investigating the Issue.
Initial Findings:
- The trusses were failing in some way based on the angle of the soffit.
- The actual loading of the roof was determined to be greater than that provided by the design risk/reward partner.
- The trusses were failing before the roof was completely loaded, before the loading even reached what was provided by the designer.
With no clear proof that one individual party was at fault, the team sent a formal email to the design/build truss fabricator (who subcontracted out the design), notifying them that their trusses were failing and asked for corrective action.
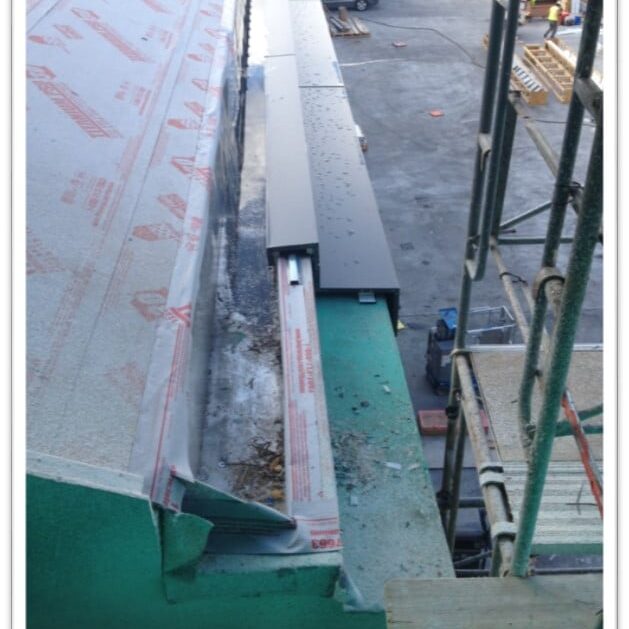
Design/Build Lump Sum Truss Contractor Response
The truss contractor provided a vague response without accepting any responsibility for the field condition and the design of the trusses.
At this point, we cannot explain the truss deflections reportedly observed in the field at the Sunnyvale Clinic, which are reportedly about three times the magnitude of the deflections calculated for full design loading. It is possible such field deflections could have resulted from truss damage, improper installation and/or overloading, but we have no evidence of any of these events having occurred.
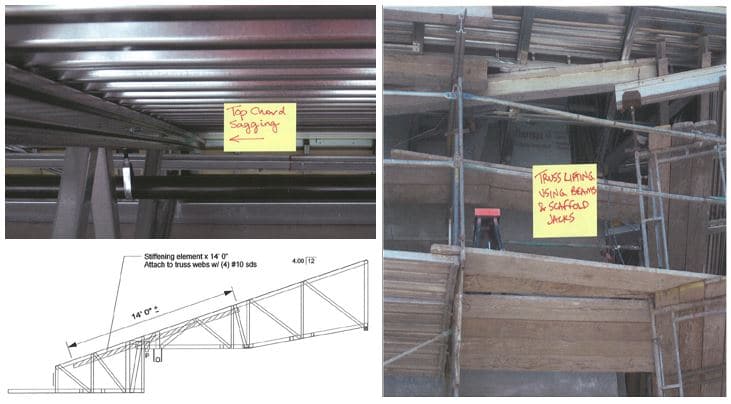
Fixing the Field Condition.
Diagnosing the problem: The team determined that the top chord of the truss was sagging as it passed the edge of the deck.
Resolving the problem: The IPD team acted quickly to implement a fix in order to keep the project moving.
- The risk/reward designer proposed adding another stud along the top chord.
- In order to get the chord straight prior to attaching the new stud, scaffolding was used to jack up the soffit from below.
- This work was done by the risk/reward skin contractor around the entire building footprint.
- The work was slow and difficult due to the decking installed over the trusses and the bracing and sprinkler lines between the trusses.
Conclusion and Results.
In an IPD contract, the owner only increases the contract value for agency issues, discovered site conditions and owner driven scope changes. This issue was a design and construction coordination issue coupled with errors/omissions which are not eligible for an increase to the contract.
Results:
- The risk/reward designer spent $40k on reviewing the issue, working with the truss contractor and designing the solution.
- The risk/reward skin contractor spent $210K fixing the issue.
- The team was paid for this $250K total out of the contingency on the project. They received overhead for the work, but no additional profit.
- The general contractor lead the investigation and resolution effort.
- The IPD team withheld the remaining contingency from the lump sum truss contractor of $40K.
- This resulted in a net impact to the IPD team of $210K that would not have been spent without the issue.
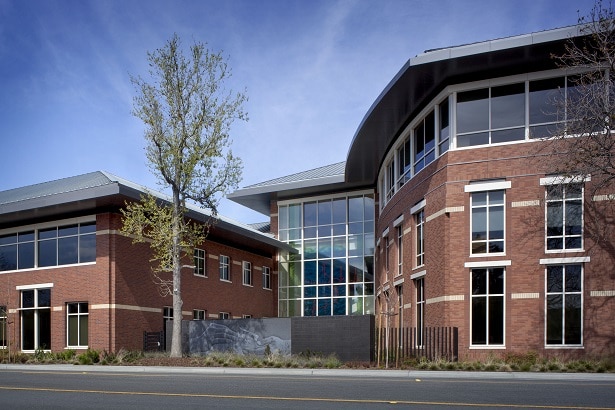
Outcome: The IPD Contract had a 35% shared savings plan for the IPD team. If the $210k was not spent, the owner would have paid out $73.5K (35% of $210k) to the team as shared savings. In this sense, the issue cost the owner $136.5k that would not have been spent if the trusses had no issue.
Most importantly, the project lost no time due to this issue. The IPD team immediately jumped on the solution instead of waiting to determine who was at fault for the sagging trusses. The IPD team, including the design and general contractor, agreed immediately that this would not be a change order to the owner.
No firm made additional profit off of the issue and there were no change orders to any member of the team for resolving the issue.