Leaving Green Footprints® is the sustainability mission at McCarthy Building Companies, Inc. As the national Director of Lean Construction for McCarthy, I often work with projects pursuing sustainability goals like LEED (Leadership in Energy and Environmental Design) certification across the United States.
Many of our project leadership teams are certified as LEED AP (Accredited Professional) or LEED Green Associate, which means we have the skills to take on large sustainability certification seeking projects. Over the past ten years, we have completed over USD10 billion in sustainable projects. To keep the LEED AP in Building Design and Construction accreditation, our LEED APs complete 30 hrs of continued education units every two years by attending conferences, workshops, or completing online lessons. LEED Green Associates complete 15 hrs every two years. As a result, our project teams collaboratively achieve more sustainable projects in the built environment working in tandem with clients and design professionals.
This article explores the mutual connections between Lean and LEED looking at the following five questions:
- Where did Lean come from?
- What does Lean mean for a general contractor?
- What are sustainability principles for a general contractor?
- What is Lean Thinking?
- Do Lean and sustainability intersect?
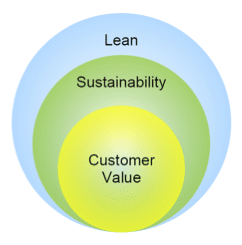
1. Where did Lean come from?
Lean is the term coined to most often describe the management philosophy and practices made world famous by the Japanese automaker, Toyota. Credit for “Lean” as we use it today goes to John Krafcik, who was part of the research team responsible for the book The Machine That Changed the World authored by James P. Womack, Daniel T. Jones, and Daniel Roos. According to Mark Graban, Krafcik said, “[Toyota]… is “lean” because it uses less of everything compared to mass production – half the human effort in the factory, half the manufacturing space, half the investment in tools, half the engineering hours to develop a product in half the time. Also, it requires less than half the needed inventory on site, results in many fewer defects, and produces a greater and ever growing variety of products.” Today, “Lean” continues to most commonly describe the methods and thinking of Toyota.
Jeffery Liker authored the The Toyota Way which summarizes years of direct research describing the principles and practices at Toyota that sustain it forward by continuous learning by solving problems with the people closest to the issues. Its members work to deliver customer value while minimizing waste. A key principle of Lean organizations includes respect for people, both their value creators and customers. Organization-wide applied lean principles significantly impact how customer value is created and delivered.
2. What does Lean mean for a general contractor?
Lean Construction at McCarthy has evolved from individual project team adoption to a holistic organization-wide implementation. Our culture is based on three guiding principles:
Genuine: Respect for the work we do and the people who do it, recognized for being honest and following through on commitments.
We, Not I: Belief in the power of teamwork and a consistent habit of sharing credit.
All In: Fully committed and a reputation as someone people can count on to do whatever it takes to get the job done.
Our values work in tandem with the six Lean Construction principles.
- Respect People
- Deliver Value
- Create Flow
- Remove Waste
- Continuously Improve
- Optimize the Whole
This synergistic set of values and guiding principles steer our work to deliver easier, better, and faster projects. We encourage many Lean tools/methods that promote continuous improvement with a focus on the Last Planner System of Production Controls, A3 Thinking/Problem-Solving, and Scrum.
We all benefit from Lean behavior and culture – improved collaboration, communication, exceptional team experiences, and learning. Lean is not a tool, task, or extra work. It is a mindset of continuous learning.
3. What are sustainability principles for a general contractor?
Environmental sustainability means that rates of renewable resources used, pollution creation, and non-renewable resource depletion don’t continue indefinitely. Human social and economic actions work in harmony with the environment. Sustainability has evolved in business to describe how organizations and people impact the environment in both positive and negative ways. The environmental impacts are from the people processes involved in materials resource utilization processes such as manufacturing and construction. Buildings change the local environments throughout their multi-decade operations. International supply chains invoke sustainability thinking beyond the physical building location. Sustainability significantly impacts resources to make and operate buildings and people living in communities around the world.
At McCarthy, our business is building, and we aim to do it responsibly, our actions directly impact those who will follow us and create new footprints on this earth. We have the responsibility to serve as stewards of the environment entrusted to us. Our commitment revolves around four principles:
- Weaving sustainability into the fabric of all company operations
- Encouraging every client and building partner to seriously consider sustainable building practices
- Bringing viable green building solutions to the table
- Educating and training our employees to give them the tools to lead the way
4. What is Lean Thinking?
Lean embodies a mindset as explained in the case study style book Lean Thinking: Banish Waste and Create Wealth in Your Corporation. A Lean perspective frames the whole set of processes that deliver a project, especially its goals. Lean practitioners focus on the big picture from the context of customer/stakeholder value and non-value adding work. Anything that doesn't support a project’s goals doesn’t add value and warrants minimization or elimination. Sustainability goals require team commitment and individual job performance deviations from standard business practices. Lean practitioners are engaged problem solvers generating sustainability project goal solutions beyond the limitations of “just another job” mindset. This highly inclusive project approach sustains empowered people continuously creating more customer value.
Lean teams are collaborative problem solvers.
A Lean mindset impacts both how teams interact and how efficiently or fast teams deliver a project. Miscommunication errors decrease as project stakeholders are engaged to work together creatively and collectively to address issues. Lean teams move further and further away from traditional siloed work to more collaborative problem-solving. Sustainable projects increase individual ownership continuously feeding on comprehensive solutions born from team members working across traditional organizational boundaries.
Sustainable “Green” construction project teams have a Lean mindset, which means that they contribute to finding a solution to minimize or eliminate waste. The project team extends beyond the people in construction trailers, design offices, and maintenance buildings. The owners, designers, builders and end users are actively engaged and included to understand how waste impacts flow and what they can do to help eliminate it. Instead of wasting time in meetings with never-ending issues logs, the stakeholders partner in focused workshops that encourage efficiency. Working together in a big room creates a shared understanding of the project issues, leads to rapid identification of areas for improvement, and builds a team of respected partners overcoming shared challenges.
The Oregon Health & Science University Knight Cancer Institute Research Building in Portland, Oregon, is a testament to the power of using an integrated project delivery approach. The project achieved a LEED Platinum certification and is paramount to OHSU’s ongoing mission to cure cancer.

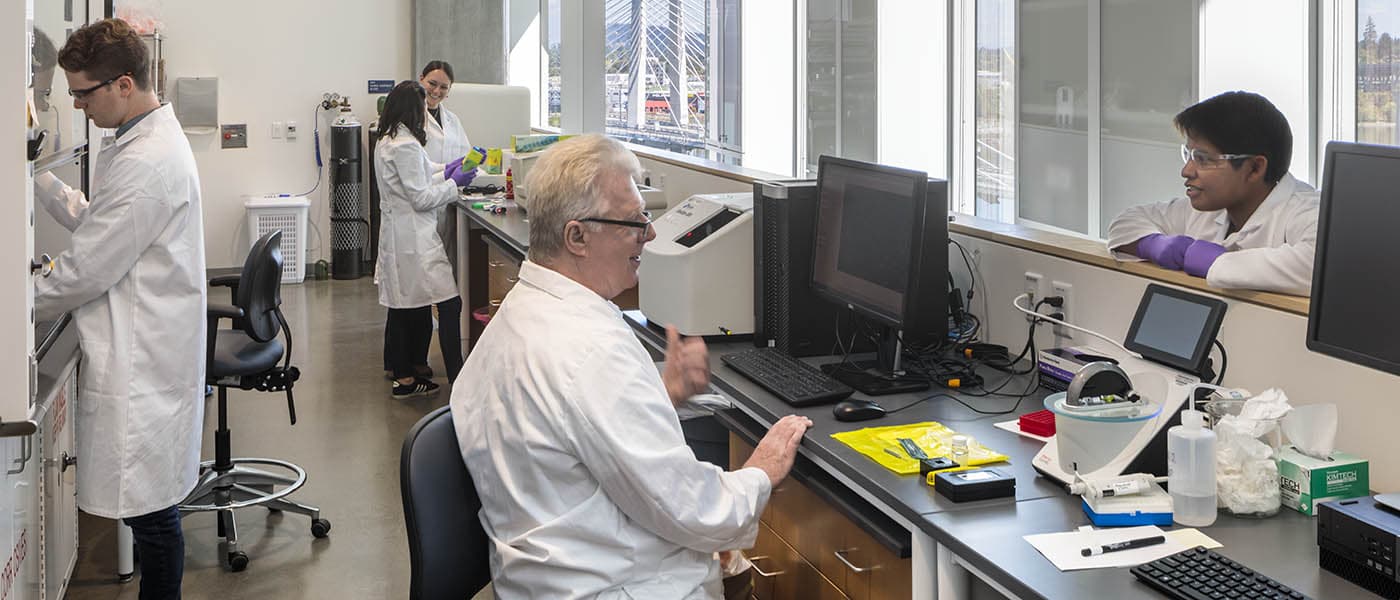
The Oregon Health and Science University Knight Cancer Research Building. Images: McCarthy Building Companies
Digital LEED plaque testifies long term performance
LEED projects require early design team and builder engagement with the customer for multiple facets of the project systems and components. The team nominates a dedicated LEED member who is responsible for all the tracking and submission in compliance with the USGBC (United States Green Building Council) standards.
Certified LEED projects may also elect to display a USGBC ‘living’, digital LEED plaque (Silver, Gold, Platinum). It dynamically displays different LEED criteria earned by the project certification level. The plaque mirrors how many credits the project has achieved as it proceeds and how it is going to perform long term in each of the following areas:
- Energy
- Water
- Waste
- Transportation
- Human experience
5. Do the Lean and sustainability intersect?
Yes, they do. Sustainable construction practices center around environmental issues that affect people. Lean Construction principles start and stop with people. Both ideologies serve what people value. The ideas are not mutually exclusive; rather they are complimentary. A sustainable building project may or may not include applied lean principles, and likewise, a Lean project may or may not include sustainable building practices although high-intensity Lean projects often do. Lean is respecting people, increasing customer value, improving flow, reducing waste, and continuously improving the whole process which compliments sustainable building practices. Sustainable project goals bring teams together to find creative solutions supporting specific environmental goals. Like in Lean, the "Green" team of people closest to the project work to identify problems and devise solutions to deliver value for the Owners.
Respecting our planet
Lean and sustainability principles are interwoven. Focusing on increasing customer value, improving flow, decreasing waste, and continuously improving builds greater respect for all project stakeholders. Lean is ultimately about people transforming their work not just making projects more efficient and sustainable; those are consequences of the people continuously improving their work. Trying to improve how you build, how sustainably you build, or a combination of both equals respecting people and our environment.
Further reading
From the LeanIPD blog
How to Empower your Lean Project Teams for Success, Part 1
How to Empower your Lean Project Teams for Success, Part 2
How to Empower your Lean Project Teams for Success, Part 3
Books
The Toyota Way, Liker, J. K., New York: McGraw-Hill, 2004.
Lean Thinking: Banish Waste and Create Wealth in Your Corporation, Womack, James P. and Jones, Daniel T., Free Press; 2nd edition, 2003.
International Lean speaker, a serial intrapreneur, Felipe Engineer-Manriquez is a committed Lean practitioner with two decades of construction industry experience. He is an active contributing member of the Lean Construction Institute and an approved instructor/facilitator. Engineer-Manriquez was honored with the Lean Construction Institute (US) Chairman’s Award during the 21st Annual LCI Congress (Oct. 14-18, 2019) in Fort Worth, Texas, for contributions to the Institute and the design and construction industry as a whole.
Felipe works with executive leadership and guides senior leaders for strategic planning and improving work processes. He works directly with regional VPs of operations to ensure safety, quality, production, and net margin enhancement. He mentors designers/engineers, and project teams across the nation. He has more than 20 years of experience in construction and more than ten years of experience in business strategy implementation. Felipe has a Bachelor of Science in Electrical Engineering, an MBA, and holds active leadership roles in the Lean Enterprise Institute, Construction Industry Institute, and other business organizations.
He is a Jeff Sutherland Certified ScrumMaster® with years of weekly sprints moved to Done and user of Scrum to lead thousands of fellow construction professionals via guided interactive learning. Felipe also currently serves as the chair of the Construction Industry Institute Collaborative Scheduling Research Team (18-362).