Humans are generally resistant to change. Change requires courage, trust, and faith. We tend to stick to long-formed habits even when we realize that they are hindering progress or create pain. Forming and establishing new habits requires effort and commitment. Sometimes, painful experiences.
How does this relate to Lean construction teams?
Many construction companies use pull planning as their technique for planning construction activities. And research shows that people who plan their work get more done.
What I’ve learned, however, is that when you take one step away from the workface in construction, many of the construction managers, superintendents, designers and engineers, are actually not rigorously planning their own work. There are few individual work planning systems in place--I might participate in planning as a team, but most people don’t roll that work up in their own individual system. This even includes companies that have a strong culture around work planning.
Are you tracking your performance?
As a presenter in front of large audiences of architects, engineers and people working in the AEC industry, I often ask my audience how many have a general idea of what they are going to be working on in a particular week.
Everybody raises their hands.
My next question is:
How many can show someone a detailed plan of what you want to have accomplished by the end of the week?
80 percent of people take their hands down.
Next, I ask how many of those who have kept their hands up have framed their work in ‘yes, no, done, not done’, and even a smaller fraction of people keep their hands up.
My last question is: how many track their performance?
There's usually only one or two people in the room who keep their hands up.
What I have found is that very few professionals in our industry are rigorous about planning their work on a regular basis.
This is a paradox because we all expect our construction teams in the field to plan their work. So why don't we do it when we step away from the team scenario?
I believe there's a couple of reasons:
- People see planning as extra-curricular, an addition to their work, and not integral to their job.
- People believe they don't have time to do the planning, because getting stuff done is more important.
Why many designers are resistant to the idea of work planning
As an architect, I understand how designers work. Often, they are juggling several projects. They make a commitment to their team in the Big Room about one project, but how they manage the rest of their work, who knows? Once they leave the big room, their commitment doesn't flow into a personal work planning system. They might plan for their team, but my experience is that less than 10% of people in our industry actually maintain a rigorous personal work planning habit on a daily and weekly basis.
As these designers are working in a collaborative environment and are making commitments to teammates on multiple projects, this is problematic. If those commitments don't end up in a personal work planning system, it is far more likely that things fall through the cracks.
The question is: Why are so many designers resistant to the idea of work planning?
Designers often believe that their work is too volatile, too unpredictable. I often hear: “You can’t control design, it evolves and just happens. We can't squeeze design into a box. It takes what it takes” As a result, when asked to make specific commitments they feel constrained and become deeply resistant.
Ask better questions
One solution is to be more mindful of how team leaders phrase their questions. In other words, to communicate and to frame our requests to designers in ways that are supportive to the nature of the design process. Shifting the focus to the creation of information for decision-making rather than insisting on design solutions is one way to do this.
For example, instead of asking “When will you be done with design?” phrase your questions differently: “Here’s the question we’re trying to answer; what kind of information on this design can you give me on this date?”
By changing our perspective and asking different questions that are supportive of the design process, we will still get the required information to move forward with the project without constraining the creative brains in the team.
In addition to the example above, these questions might be helpful next time you want some information from your designers:
What kind of questions can we answer about the design on a specific date?
What kind of questions can we answer in a certain timeframe?
And, apart from asking better questions, it is crucial for all Lean construction team members to establish a personal work planning habit to become more productive and perform better as an individual, allowing them to be more reliable promisers to the team.
Solutions for work planning systems
Instead of trying to handle multiple to-do lists, which do not have a time component, or numerous unstructured sticky notes, I encourage team leaders, managers, and designers to start a personal work planning habit. This doesn’t need to be complex, there are a range of simple solutions, both analog and digital.
When I teach work planning, I encourage people to start with a paper-based version. Paper is more flexible and less rigid than digital solutions. And there is something about the nature of crossing a task off on a piece of paper. It has a different feeling about how you commit and measure your work.
Analog systems include sticky-note-based Kanban systems (today, this week, next week, future or To Do, Doing, Done), bullet journaling, and many more.
It doesn't really matter which system you choose as long as you start implementing some kind of personal work planning habit. The first step is to dedicate one hour a week, preferably on Friday afternoon or Sunday evening, to plan the next seven days. Answer the question: what are the tasks that I want to have done by Friday afternoon?
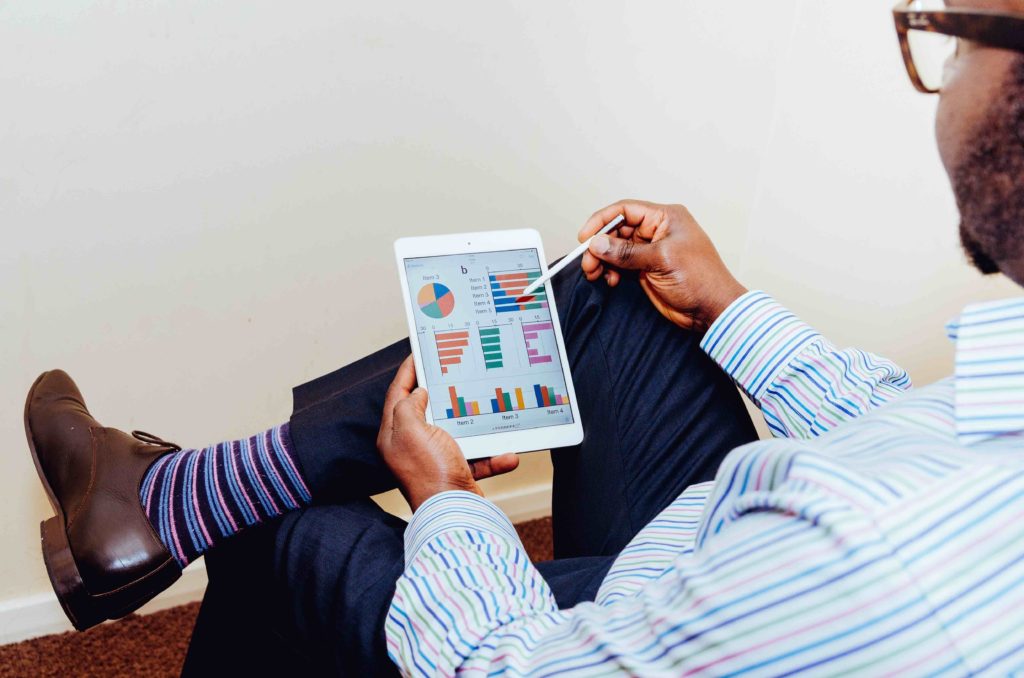
Why tracking variances is crucial
At the end of the week, it’s important to reflect and measure your performance of that system by exploring the following questions:
- How did it go?
- Which tasks did not get done and why?
Tracking variances (the reason why a task doesn’t get accomplished) is crucial to understand the systemic underlying problems in your work. If over time you discover that the main reason for not getting tasks done is that you are always waiting for information from others, you have identified a root cause and can reorganize your work accordingly. Or the relationships with the people from whom you are waiting for information.
The benefits of work planning match the frustrations
In my presentations, as part of a quiz, I ask the audience about the most frustrating things in their work.
Many people reply: changing priorities, getting side-tracked, missing information, or lack of communication.
I then ask: What might be the benefits for someone who plans and measures their work?
Perhaps not surprisingly, the answers I get about the benefits of work planning are pretty much a 1:1 match for the frustrations people experience in their work, and yet, personal work planning is not accepted as an important and integral part of success in their work. An interesting fact.
If more people understood that planning their work allowed them to be more productive and get more done, if they saw work planning as integral to their work, not as incidental or in addition, they could experience a real difference.
Related articles
What Every Lean Project Team Should Know About Scrum
Work Planning Systems
Franklin Planner
Bullet Journal
Kanban vs Scrum
Swimlane Diagram
Markku Allison, AIA, has over 35 years of experience both as an award-winning designer and as a thought-leader on design and construction industry transformation issues. His background as a practice owner and industry subject matter expert with strong relationships across disciplines and organizations uniquely positions him to assist in shaping responsive strategies to force driving change in business and culture today. In his current role, Markku heads up Chandos’ innovation initiatives. He served as president of the Integrated Project Delivery Alliance (www.ipda.ca) in Canada which has published “IPD: An Action Guide for Leaders,” several influential IPD research studies and provides IPD training for industry. Markku also held positions at the American Institute of Architects, where he was a joint content editor in the development of the AIA’s “Integrated Project Delivery: A Guide”.