Are you a project manager who is still dealing with static PDF construction drawings, outdated Excel sheets, duplicate data entry, and mistakes that happened because contractors didn’t ask questions or didn’t have all the necessary information to complete their jobs properly?
Let’s look at an example. You are building a research facility. It is composed of structural steel, rooms, doors, walls, floors, ceilings, sinks, toilets, ducts, lighting, pipes, and so forth. Some of these objects are built in the course of construction, such as the walls, rooms, or ceilings. And other objects are procured and installed, such as beds, monitors, and furniture. Tracking both built and installed objects are important to the ultimate completion of this facility.
What would your workflow look like if you had an intelligent construction drawing software tool that creates an easy-to-access, robust system for all involved contractors to retrieve critical information about any object onsite with one click?
How can you make the construction process more efficient, maximize the value of people’s time and efforts, and generate profits for all involved parties?
The answer is Intelligent Construction Drawings, which eliminate non-value-adding steps, aka waste, and fulfil several objectives of lean construction.
Here are five shifts for project managers to advance lean construction:
- Organize your project data around objects
Let’s look at a door, which is a typical object in a construction project. The architect builds the door in a virtual model. Someone has to price and order that door. Another contractor is going to deliver and install the door. An inspector will check that door for safety and functionality. Eventually, the door will be used by the people who live or work in the building.
The traditional way of organizing the data for the door is in Excel sheets or cloud-based equivalents. It is a siloed approach that uses numerous lists for unique purposes, specific solutions, speciality trades, and different stakeholders. This highly inefficient approach leads to a waste of time trying to locate information when needed. It is also error-prone as information in these siloed environments gets out of sync and results in mistakes and subsequent rework. These inefficiencies are counter to the principles of lean construction.
Whereas objectifying your project data means giving it a correlation by changing the organization structure from a bunch of lists for one single door to a virtual container for the object.
Next, you connect all the tools that track things about that door with your data container in the cloud which everyone can plug into.
For example, you may have 1,000 submittals for your project, but the only submittal that should matter to you when you're working with the door is the one about the door. So to object-orient your project data means that when working on the door your information is automatically filtered to only retrieve the information you need, which is the benefit of this optimized organizational system.
Similar to how the Rosetta Stone enabled the translation of previously undecipherable texts, organizing project data around objects provides the key to unlocking communication and collaboration among previously siloed stakeholders. Objects unlock a new way of communication by creating a translation layer that makes the information relevant to the entire team. This organization system creates a unique home for project data so that everyone works with the same information in one central document. It is universally understood, universally functional, and easily accessible
Inertia Systems, for example, uses an interactive map with clickable objects. Let’s look at the door again. Whether you are the owner, the architect, or the painter, you can click on the door and every bit of information that was ever entered about this door will come up. All your updates to the status of the door will be added. Even if contractors are on the project for one day only, they can use this interactive map to write a note about their work on that specific door, take a photo, and add their invoice.
And someone else who joins the project two years later can click on that door and retrieve all the information that was ever entered and added to that specific door.
2. Improve your current operating procedures through integration
How can you incrementally improve your current operating procedures? Based on my experience with technology adoption in the construction industry, instead of large shifts, incremental improvements that can be layered on top of existing operating procedures and introduced through seamless integrations have a better chance of producing lasting change and improvements.
We all know that most humans are inherently change-resistant, and construction is a very fragmented industry. For a construction team to change their behaviour takes time, discipline, and effort, and bears a huge cost factor.
What are your choices? Is it worth making the shift with the cost and risk that comes with it? Or, can you incrementally improve your existing operations?
In most cases, it will be easier to improve your existing commitments and choices. So you can immediately disqualify solutions that don't integrate or that require a huge commitment to shift.
A thoughtful integration of a new solution into existing processes and procedures will add value to your existing operations without bearing high risks or substantial costs.
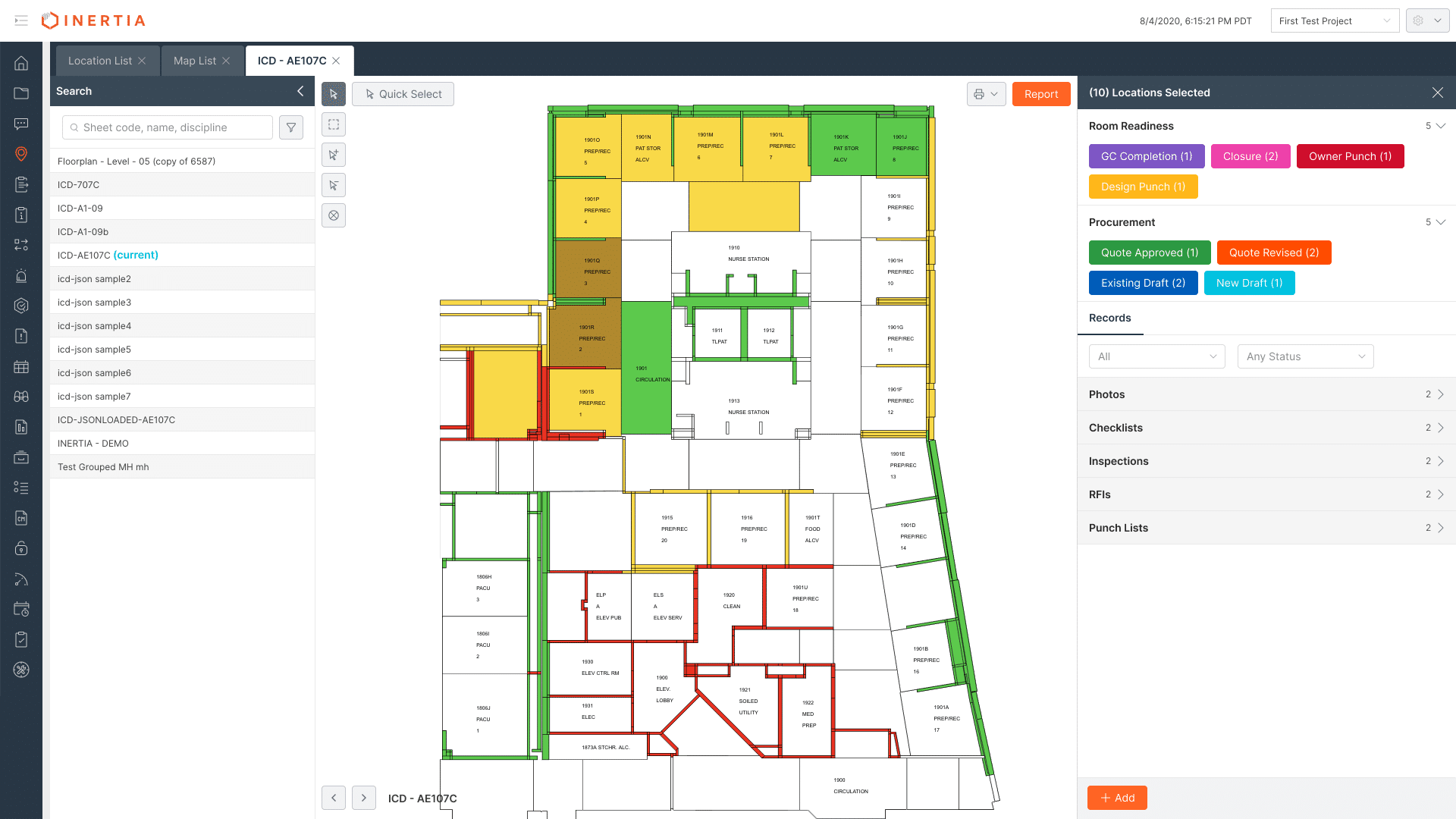
Image: Inertia Systems
3. Visualize all project information in intelligent documents
A typical construction team consists of many different stakeholders in varying degrees of sophistication and skill sets. You have tradespeople hanging drywalls and swinging hammers, and you have the architects and engineers who model the building in 3D. Everyone has their specialized skill set, and they are all critical to getting the project done.
The question is how can you universally connect them all? The common ground is the construction drawings. No matter what language you speak, we can all look at a map of a building and click on a door, a toilet, or a sink and understand what it is and what it does.
At Inertia, we work with color-coded maps using red and green as universal colors. A green door indicates that everything is going to plan with our door. If our door appears in red, it means there is a mistake, an issue to resolve. And the project manager can just click on it to see all data entries about the door that have ever been made. Whether it is a cost document, a scheduled document, an RFI, any planned event that's off track, any unplanned event that's off track, you can simply identify it by clicking it. And this is a significant time saving and a much better and leaner way to communicate.
This tool is a valuable asset for the project manager or general contractor who can see with one click how many issues one room has. Ten red items means there are ten issues in that specific room, which suggests that the whole room needs to be reviewed. If only one sink appears in red, the contractor who installs the sinks knows which specific sink to fix.
In summary, visualization through one interface helps all involved parties to be on the same page when it comes to mistakes or issues that require attention. It saves time and energy. It values people’s efforts. It is more efficient.
4. Remove all non-value adding steps
To remove non-value adding steps we first need to identify what they are. This sounds pretty obvious, right? The problem, however, is that people don't know what they don’t know. Meaning that we don’t always know that we have a problem until we see a way to do something better or faster. Problems are not obvious until we start asking.
There are a lot of non-value adding steps in construction. There's duplication of records, there's duplication of efforts. There's just a lot of time spent doing things manually.
That doesn't have to happen with the right technology. But teams don't always know about this new technology, or have perspective beyond their scope so they keep doing what they have always done. The status quo is predictable, it works, there is no margin of error. So you keep maintaining the status quo. You stay in your comfort zone. Unfortunately, it also means you won’t improve or get a better result.
Let’s look at some examples of non-value adding steps.
When you are spending three hours a day highlighting and color-coding pictures to visualize and better communicate that information to your team, there is an opportunity to innovate simply by using new technology.
With a click of a button you can update and communicate accurately all the necessary information in real time to thousands of users.
Another example is duplicate data entry. There is known duplicate data entry, which happens when you have to pay people to enter information into three different software tools because these tools don't speak with each other.
But there is a much bigger problem, which I call the unknown duplication. This happens, for example, when different people ask the same question on a project.
Five different people ask the same question once but the person who is answering has to reply five times with the same message, which means they are wasting their time because their answer is not communicated simultaneously to the entire team. And because five people asked that question, it is very likely that more people will have the same question. What is even worse is when the next person doesn’t ask and creates a mistake on the project because they just were not aware that there was a problem.
And so if you connect your data better through technology, you remove all those non-value adding steps, such as duplicate and triplicate data entry, non relaying of information, and duplication of efforts to fix mistakes.
5. Learn your lessons by appreciating people’s time
Generally speaking, any software used on construction projects should gather information in a way that supports lessons learned and share these with the team. This also applies for mistakes that happen onsite. The goal is to learn from the mistake and communicate to the team how to avoid the same mistake going forward.
Unfortunately, more often than not, we see mistakes being repeated because the lessons were never communicated. It is one thing to make a mistake because people are just negligent.
But making a mistake because of a lack of communication or training is a completely different thing. This situation becomes even more critical if we look at workforce shortages, new people onboarding, or senior people exiting.
How do you transfer knowledge in construction teams?
Where do you create a central knowledge base that captures all the lessons learned and effectively communicates them to the entire team?
Let’s look at our door example again. If on door #100 you found a problem, you need to fix it, update the notes for door #100 and then post your answer to all the other doors (objects) so that anybody who will work on any one of those doors in the future can find what you entered. They will instantly see how a specific problem was solved, which means they can use this knowledge to avoid the same problem on all of their doors.
You can apply your lessons learned to all the doors of the project with one click. A contractor who opens the object for door #100 five years later will see your lesson learned. So even if it was his first day on the job, this person would find valuable knowledge on how to get his job right from the start.
In summary, knowledge transfer and lessons learned are vital components to avoid waste in construction projects. The right technology allows owners and project managers to maximize their investment in human capital, minimize waste through intelligent construction drawings, and share lessons learned across the entire organization.
Summary
Lean construction is about reduction of waste. How do you reduce waste, communicate efficiently, and connect data so that construction project teams become more efficient?
We believe that organizing data around objects is the key to eliminate waste and increase profitability of construction project.
This approach is universal, efficient, interactive, and lean.
Interested in learning how intelligent construction design will improve your project? Contact Inertia to schedule a demo!
Feature image: Inertia Systems
Related articles
Concert Enables Digital Project Delivery and Trusted Data Exchange for Lean Project Teams
Reducing Soft Waste in Construction with Common Data Exchange
Overcoming Resistance to Change
Matthew Hudelson is the Founder of Inertia Systems. Since 2010, he has worked alongside builders, owners, inspectors, architects, and other project team members to learn how Inertia tools and workflows impact the challenges on construction sites. In turn, Inertia provides intelligent construction software to eliminate waste and improve efficiency throughout every step of the construction process.
No matter how large the team, Inertia’s intelligent construction drawing software delivers visually connected information, automatic updates and notifications, which helps reduce waste on construction sites, and improves construction workflow, and project outcomes.
Clients include the Parnassus Hospital, UCSF Medical Center, the SoFi Stadium, and Stanford University.