What if you as a project owner in healthcare could build faster, control your supply chain, increase the quality of the finished product, and lower costs by utilizing an industrialized construction approach?
Sounds too good to be true? Read on.
At Mark III, we are fuelled by our vision to lead the evolution of the construction and have been working on a series of internal research and development projects, called Project Mountain (PM), since 2017.
The objective of Project Mountain is to disrupt the traditional construction process by standardizing design, streamlining material procurement, and leveraging prefabrication and manufacturing to build better, faster, and cheaper.
In this article, I will share our findings from Project Mountain.
Phase 1: Simplify construction with manufactured standardized kits (MSK’s)
During the first phase, we built a single medical exam room utilizing manufactured standardized kits (MSK’s), with minimal prefabrication.
The Project Mountain team began by virtually modeling the exam room for all trades – mechanical, electrical, plumbing, and wall framing. From there, we produced detailed step-by-step instruction manuals for every task required to build the exam room, from metal-stud framing to paint and finishes. We created a precise BOM to minimize material waste and implemented a just-in-time schedule to provide the crew each day only with the materials, tools, and instructions they needed for that day’s work.
Results: Completion of the first room in 10 days
The first room installation was completed in 10 days. We had captured all issues resulting in waste during each phase in an issue log, which allowed us to eliminate repeat mistakes. We also created and implemented countermeasures for each recorded issue in subsequent phases.
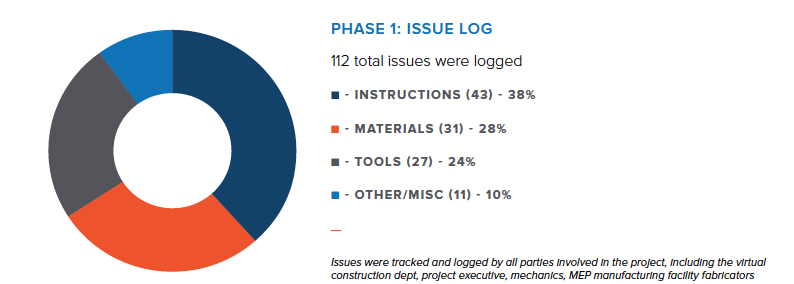
Phase 1 at a glance:
Estimated install hours
160 hours (10 days)
2 non-trade specific mechanics
Labor breakdown
Virtual Construction: 393 hours
Manufacturing & Install: 322 hours
- 162 factory hours
- 160 installation hours
Total phase hours: 715
Source: Makayla Oei, Mark III Project Executive
Phase 2: Improved instruction, tools, and logistics
To build the second exam room, the team repeated the same process used for Phase 1 and implemented countermeasures into the kits based on issue log findings. These measures included improved instructions and corrected materials, tools, and logistics.
However, phase 2 was affected by weather impacts. Cold temperatures delayed the drywall mud and paint drying time. While the field installation hours remained the same, the team did see a sizable reduction in design/virtual hours and fabrication time.
Results
Following the same processes from Phase 1, the second room installation was also completed in 10 days.
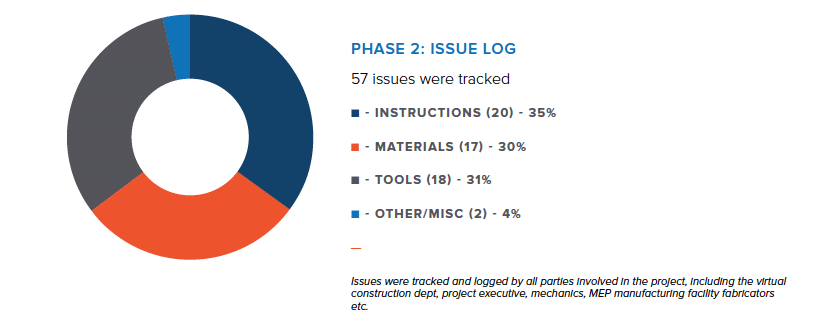
Phase 2 at a glance:
Estimated install hours
160 hours (10 days)
2 non-trade specific mechanics
Labor breakdown
Virtual Construction: 141 hours
Manufacturing & Install: 237 hours
- 77 factory hours
- 160 installation hours
Total phase hours: 378 hours (almost cut in half compared to Phase 1)
Source: Makayla Oei, Mark III Project Executive
Phase 3: Two exam rooms built in tandem
During the third phase, we built two exam rooms utilizing an enhanced process based on the implementation of countermeasures put in place from the Phase 1 and 2 issue logs. Rather than utilizing MSK’s for all material brought to the build site for the two non-trade specific mechanics, we delivered pre-manufactured wall panels. Each manufactured wall panel was delivered complete with multi-trade utilities including prefabricated in-wall assemblies for electrical, low voltage, and plumbing systems.
Elements that changed:
- We built two exam rooms in tandem
- We increased the level of manufacturing
- We utilized a new team of two non-trade specific mechanics to ensure that we did not overlook issues due to a "seasoned team".
Results: Completion of installation in 6.5 days
Utilizing a manufactured approach allowed the team to finish installation in just 6.5 days, reducing the installation schedule by 35% compared to Phase 1 and 2. Additionally, the virtual construction hours were reduced from 393 to 60 with the likelihood that this value will further decrease with an increase in standardization.
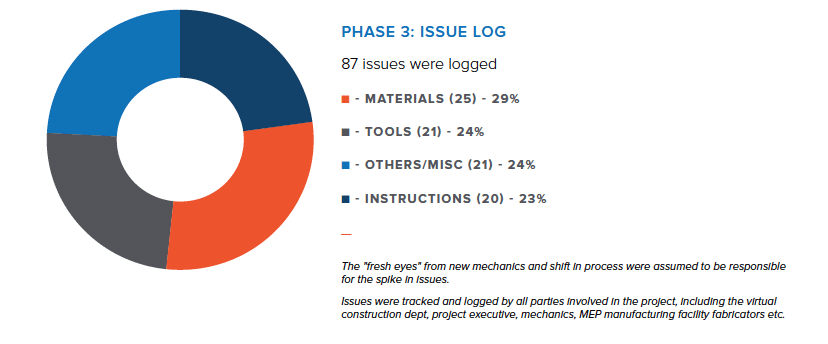
Phase 3 at a Glance
Estimated install hours
160 hours (10 days*)
2 non-trade specific mechanics (new team)
Actual install hours
6.5* days
Labor breakdown
Virtual Construction: 60* hours per room
Manufacturing & Install: 129.5* hours per room
- 25.5* factory hours per room
- 104* installation hours per room
Total phase hours
189.5* hours per room
* Hours divided by 2 to account for hours per exam room
The future of construction
By standardizing design and utilizing a manufactured approach to build a complex medical office building exam room, the Project Mountain team was able to reduce total hours spent by 71% from Phase 1 to Phase 3*.
In addition, utilizing multi-trade manufactured wall panels during Phase 3 enabled the team to reduce on-site installation by 35%, thus illustrating that manufactured MEP wall panels are more efficient than fully kitted raw materials for the metal-stud framing and in-wall utilities.
Hourly rate breakdown
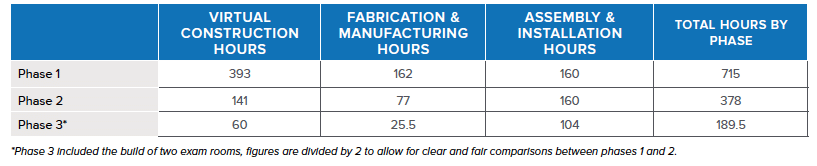
While the team did experience schedule improvements for the manufactured MEP wall panels (complete with in-wall assemblies), there were no recorded improvements for other tasks required to complete the exam room, such as drywall, drywall taping, drywall mud, texture and paint. These specialized tasks proved to be the most challenging for the mechanics and did not yield any reduction in hours over the three phases.
Moving forward, these specialty activities will be subcontracted in order to ensure that all possible cost and schedule savings are captured.
Challenging the status quo in construction
At Mark III Construction, we will continue to apply these practices and findings to projects in the field. This approach vertically integrates the full scope for all trades: mechanical, electrical, low voltage, plumbing, piping, and framing. MEP wall panels will be manufactured in Mark III's MEP Manufacturing Facility before being shipped to the job site, which
improves the quality of the product, simplifies project design, reduces waste, and increases project predictability for all stakeholders.
To follow our progress on challenging the status quo in design and construction, visit our website.
Makayla Oei is the director of preconstruction for M3 Components (M3C). She has over 15 years of industry experience, from project engineer to project executive Makayla has overseen projects from concept to completion. Since 2017, her focus has been building a productized approach to healthcare construction. She has completed multiple rounds of research and development, known as Project Mountain, and has successfully completed multiple projects utilizing M3C products.