Have you ever felt you did everything right on your construction project?
You hired a design firm familiar with your campus and the project type. The general contractor joined the project early and did numerous constructability reviews. The design incorporates feedback from the construction team in the permitted documents. The trades came on board early, they had a chance to model the project, and buy out started early to beat any supply chain concerns.
Why then, you keep asking yourself, is my project struggling to hit its schedule milestones?
The end date for the project keeps moving out and you are not sure when it is going to finish.
This article explains why Just-in-Time Deliveries, Location Based Scheduling, Takt Time Planning, and the Last Planner System ® can be the answers to your questions.
Cost and schedule overruns are the norms in construction
According to data from a global McKinsey study published in 2016, complicated projects like Oil/Gas, Infrastructure and Mining had an average of 20 percent delay from the baseline schedule.
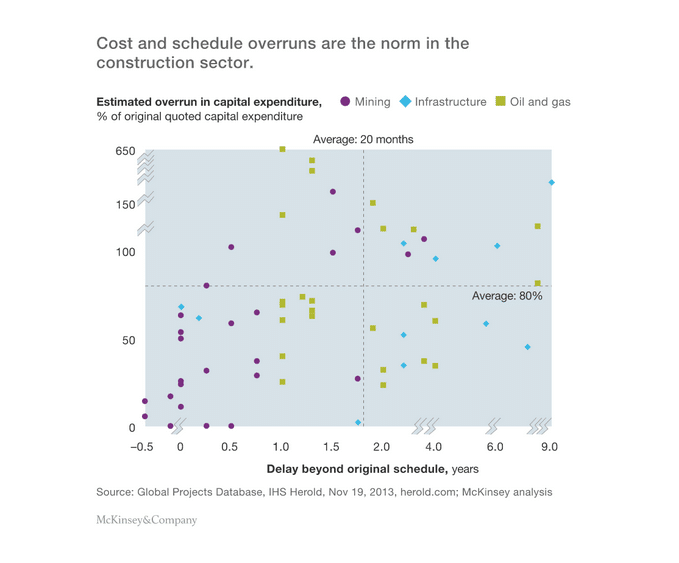
To understand why projects finish late, even if they are well-coordinated during design, let’s look at our traditional processes.
The majority of construction projects have a regularly scheduled meeting with the Owner, Architect (or Engineer), and Contractor where schedule and budget is discussed. Most of the time is spent reviewing the schedule to understand why a project is behind schedule and discussing what can be done to get the project back on schedule. We talk about overlapping tasks, working in multiple areas and of course - overtime and double shifts.
So what’s wrong with that?
What most fail to realize is that schedule and budget for a project are lagging indicators of how the overall project is performing. A schedule which shows the project finishing late is most likely due to the project not performing at some point months or years in the past. If a project is trending over budget, it is usually because of changes, incomplete design and misunderstandings that took place months or years prior to the meeting when the budget is reviewed.
Focus on construction as a system
To reliably deliver construction projects on or ahead of both the schedule and the budget, it is important to manage the inputs to the system, the levers which cause a project to go over budget and finish late. Schedule and budget are outcomes of a system, lagging indicators of project performance. What then are the inputs to a system, and what can we do to increase our focus on those inputs so we can drive the results we desire out of the system?
One of the most critical ways to get both a reliable schedule and a reliable budget on a project is to focus on flow. Flow of work on the project site, flow of materials to the project site, flow of information to and from the field. In short, through the creation of flow on projects as an input to the system or as part of the overall system design, schedule and budget can be driven for superior outcomes.
To drive flow on a project at the field level, it is important to focus on construction as a system with inputs and outputs. Flow can be achieved with a system of Just-in-Time Deliveries, Location Based Scheduling, Takt Time Planning and the Last Planner System ®.
Just-in-Time Deliveries
In order to control the amount of inventory on a construction site and within the area of work, it is imperative to limit the amount of material that is delivered when it is not needed. A team should strive to develop a supply chain to the project site that delivers material and equipment just-in-time, not before and not later than it is needed to perform the work. By careful control of deliveries and management of that material and equipment on the site, it is easier to keep the site clean and free of clutter. This will allow for work to be safer and requires less labor due to double or triple handling of material.
To set up a true Just-in-Time delivery system for a project, the workers and their suppliers need to know what material and equipment is required where and when. Material and equipment can then be pulled to the site when it is time to install it so it does not sit unused taking up space and impeding other work.
Location Based Scheduling
It is challenging to accurately predict when the teams need specific material and equipment unless there is a detailed schedule of what work is happening and when it is happening. Location Based Scheduling (or Planning) is about breaking the project site down into areas. Specific work packages, such as mechanical overhead or electrical inwall, are then scheduled to occur by area on a project. For example, Mechanical overhead might be taking place on the South side of the 5th floor while Electrical inwall is taking place on the North side of the 1st floor.
Once work is made specific and broken down by area, the crews can plan the material and equipment they need for the upcoming areas and order them from their supply chain.It becomes possible to take off the quantities for the specific area that is coming up in the schedule and pre-package the material and equipment for delivery to the site and directly to the area. It is important to understand not only what area is coming up next and what work it includes, but also when that area will become available to a specific trade so they can start their work.
Takt Time Planning
In order to accurately predict when an upcoming area will be available for work and free from the previous trade, it is important to get reliability around the schedule and sequence of trades. Takt means beat in German, and is similar to the beat of a grandfather clock. If the work of each trade in each area is scheduled for the same amount of time, then it becomes easier to predict when areas will be completed. For example, a building that is broken down into two areas per floor (north and south) can plan for each scope of work to take one week per area. This would be a Takt of one week. When a trade finishes in their area, they move to the next area and the trade behind them moves into the area they are vacating. In a perfect world, the project will move like a fine watch with trade crews receiving exactly what they need right before they start work in an area. They will install that work completely within the Takt time and be ready to move to the next area. In reality, many issues can cause the work to speed up or slow down, so it is important to manage and monitor the work closely with real-time feedback.
Last Planner ® System
According to the Lean Construction Institute at Leanconstruction.org, “Last Planner ® System (LPS) is a system for project production planning and control, aimed at creating a workflow that achieves reliable execution, developed by Glenn Ballard and Greg Howell, with documentation by Ballard in 2000. LPS is the collaborative, commitment-based planning system that integrates should-can-will-did planning: pull planning, make-ready look-ahead planning with constraint analysis, weekly work planning based upon reliable promises, and learning based upon analysis of PPC and Reasons for Variance.”
The system is designed specifically to create reliable work by involving the people doing the work (the last planners before the work is actually performed), creating specific commitments (usually on a weekly look ahead), tracking if the work was completed as planned and capturing the reasons (variances) why work wasn’t completed with the goal of learning and implementing countermeasures to prevent future break downs.
With a successful implementation of LPS, a team is able to carefully monitor the work of each trade within each specific area of work and make corrections on a real time basis. This ability to track and adjust is crucial to keeping the individual trades on takt within their areas. When inevitable issues arise, the team is able to quickly diagnose the root cause and come up with a solution to the next area so that the work is not delayed.
Conclusion
Assuming a project team is on board early, coordinated the project well and is ready to fabricate from the design model, your project schedule and budget is still at risk.
Reliable (or unreliable) budgets and schedules are outputs of the construction process. To increase reliability of schedule and budget, it is important to view onsite construction as a production system. To manage and improve the system, one must focus on the inputs instead of the outputs of that system. Success of a production system is dependent on how well that system flows. To create flow, one should focus on inputs to the system, specifically Just-in-Time Delivery, Location Based Scheduling, Takt Time Planning and Last Planner ® System.
Coupled together, these concepts and strategies will allow for a smooth flow of material, equipment and labor on the construction site. With a smooth flow, the work will be more productive, safer, quicker and ultimately result in equal or higher quality with less rework.
Later posts will dive deeper into each of these concepts with practical examples of implementation.
Related articles
Are you Leveraging the Power of your Construction Team?
Getting Smart with Pull Planning in Design
James is an expert in the set-up and structure of large, complex capital projects using Lean and Integrated Project Delivery to drive highly reliable results.
He has negotiated IPD contracts and delivered over $650M in complex healthcare projects as an Owner's Representative with multiparty contracts, aligned team incentives and collaborative delivery models.