“Soft Waste” in the construction supply chain is caused by bad communication, duplicate data entry, unclear responsibilities, or human error, is one of the eight forms of waste in lean manufacturing.
Duplicate data entry was also one of the five pains identified in our 2019 report for ELECTRI International where we looked at how a Common Data Exchange (CDX) can improve RFI efficiency and insights for electrical contractors. The CDX Playbook allows project stakeholders to communicate standard procedures and interoperability requirements with digital literacy. It documents effectively who, what, when, and where as it relates to each RFI stage and workflow activity from the trade contractor’s perspective.
I believe that the future of RFI integration lies in our ability to coalesce standards from each trade contractor, the general contractor, the architect and their engineers, and - of course - the owner. Beyond simply visualizing RFI data, which it exchanges through traditional means, the new best practice should be for RFI stakeholders to establish bespoke workflow standards that meet industry-wide Key Performance Indicator (KPI) standards that are derived from the lean community.
Managing waste starts by measuring it, which could be perceived as an activity of waste. If delayed responses and unanswered RFIs pose such a significant risk to the trade contractor, how do they properly document the time lapse between key status changes without requiring added manual data entry? By establishing more efficient exchange workflows using technology solutions that automate the reporting of these critical timestamps, all stakeholders can more easily perform root cause analysis or look for leading indicators in the data.
The 5 tiers of the CDX Playbook
The following baseline risk tiers are proposed to help project delivery stakeholders establish the critical thresholds where RFI data passes responsibility from one stakeholder to the next. Each time the RFI document moves between tiers, the project team will decide what data is required, who is receiving it, and how they will measure it.
A mock collaboration between industry and technology SMEs conducted in May 2019 delivered three recommendations to measure RFIs effectively. This includes measuring the impact tier 1-4 that an RFI reaches in its lifecycle, the project phase in which it originates, and the time lapse between key status changes.
The CDX framework establishes a total of five document tiers from 0-4. Following the “v”-system engineering model, project design begins with Tier 4 and ends with tier 0. Once the project crosses the boundary of realization from design to construction activities, the tier progresses upward from 0 to 4.
Tier 0: at the bottom is Tier 0, representing the project Common Data Environment (CDE). Signed contracts, permitted design documents, and approved submittals are all examples of ‘posted’ documents that should be accessible to all project stakeholders and stored in the Tier 0 CDE.
Tier 1: The initial question raised from a trade contractor is considered a Tier 1 (informal) RFI. If the RFI response does not require a change to the permitted design, it remains a Tier 1 RFI.
Tier 2: After receiving the Tier 1 RFI from a trade contractor, the general contractor will review it to determine if the RFI indeed requires a response or change from the designer of record. When the designer responds with a supplemental document or revision to the design, it is now classified as a Tier 2 RFI.
Tier 3: If the designer’s response to the contractors results in a cost or schedule impact to the project, the RFI triggers a Potential Change Order (PCO) document and the attached RFI documentation is now classified as a Tier 3 attachment.
Tier 4: The greatest impact an RFI can have on a project - and thus it’s significance - occurs when the owner recognizes the true cost or schedule impact of an RFI when it emerges as a Tier 4 Change Order. While the RFI document itself is not typically included as part of the Change Order document, it was certainly at the root cause of it, and thus should be measured and managed.
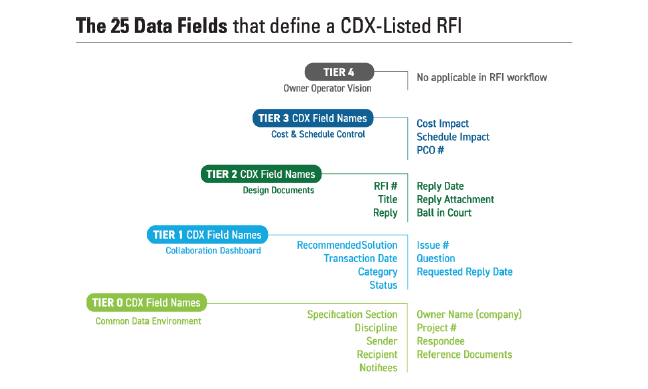
List of 25 RFI standard data fields, broken down by impact tier. (Source: Improving RFI Efficiency & Insights through a Common Data Exchange)
RFI integration opportunities
Historically, the RFI has been demonized as a “bad” document that should be eliminated from the construction supply chain. This misunderstood communication tool for design change management can evolve in the digital age to have greater flexibility and automation. Interviews with operations managers, RFI coordinators, and external collaboration stakeholders revealed five primary opportunities to improve RFI data integration and insights:
- HOW MIGHT WE … auto-reference Tier 0 documents to a Tier 1 RFI...IN WAYS THAT … leverage hyperlinks and metadata to identify drawing or specification number, location, and an associated reality capture data … SO THAT … reference documentation maintains standard metadata tags and direct link accessibility when authorized?
- HOW MIGHT WE … streamline the capture and exchange of Tier 1 RFI documentation prior to external exchange … IN WAYS THAT… eliminate the duplicate entry between field solution and office platform … SO THAT … RFI documentation quality and efficiency is measurably improved?
- HOW MIGHT WE … post RFI data from one stakeholder’s system to their customer’s PM platform … IN WAYS THAT … automatically translate required fields from Tier 1 to Tier 2 from pre-defined logic ... SO THAT … duplicate entry and loss of data between systems are reduced?
- HOW MIGHT WE … notify the trade contractor in their Tier 1 PM platform when a Tier 2 RFI passes responsibility (or ball in court) … IN WAYS THAT … can be customized to individual or project requirements … SO THAT … notification settings are neither too much nor too little?
- HOW MIGHT WE … categorize RFI responses that anticipate a cost or schedule impact … IN WAYS THAT … auto-generate a Tier 3 Potential Change Order (PCO) number and reference associated RFI documentation … SO THAT … Tier 4 Change Order requests are explicitly accurate and irrefutable?
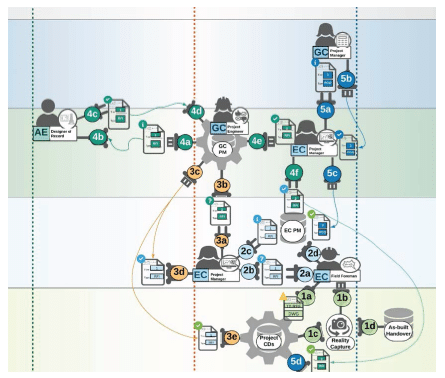
Detailed CDX playbook for RFI including activity ID and type (Source: Improving RFI Efficiency & Insights through a Common Data Exchange)
The four boundary phases of the CDX framework
In a perfect world, there would be no RFIs and everything would be reliable and accessible from the Tier 0 CDE. When there is not an IPD contract in place, trade and general contractors are incentivised to manage the risk they are exposed to by effectively documenting their right to compensation when late design changes occur.
When it comes to measuring the quality of RFI collaboration on a project, project teams should consider:
- What tier did the RFI ultimately reach? (lower is better)
- How long did the RFI spend in each tier? (shorter is better)
- Which phase of the project lifecycle did the RFI originate from? (earlier is better)
The CDX framework establishes four distinct phases across a project’s lifecycle: Plan, Design, Build, and Operate.
The four phases of project delivery are separated at three clearly defined boundaries: Alignment, Realization, and Certification.
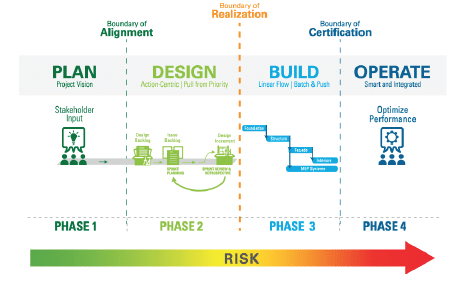
Illustration: ELECTRI International: Improving RFI Efficiency & Insights Through a Common Data Exchange
A project’s contract delivery method will have a significant impact on where the boundary lines are drawn between phases. This should be a collaborative effort during project kickoff, but doesn’t have to be. Ultimately, there should be a defined protocol for RFI correspondence, including the conditions of satisfaction for an RFI document to cross over each boundary - depending on tier classification.
Examples of each boundary condition have been defined below, as it relates to different contract delivery methods.
Boundary of Alignment (BOA)
The Boundary of Alignment separates the Owner's Tier 4 requirements (phase 1 - Plan) from design and coordination activities (phase 2 - Design) that occur between the Construction Manager in Tier 3 and the Designer of Record in Tier 2. If the Owner fails to clearly define their COS requirements and priorities in Phase 1, it generates waste through needless design and coordination iterations in Phase 2.
On progressive Design-Build and Integrated Project Delivery (IPD) contracts, the BOA can occur as early as the schematic design. On traditional Hard Bid contracts, the BOA occurs when the client accepts the contractor’s final bid. Unless the team agrees to IPD, it is difficult for any contractor to propose any RFIs or have influence during Phase 2.
Boundary of Realization (BOR)
The Boundary of Realization is a moving target between the end of Phase 2 - Design and the start of Phase 3 - Build. It occurs at the point where proposed design is “officially” released for physical procurement. This point is typically represented by return of reviewed submittal documents with a stamp marking them “approved”. RFIs that are asked and answered prior to the BOR produce less overall impact on the fabrication supply chain, because nothing has actually been fabricated.
In Hard Bid contract delivery, RFIs asked and answered after the BOR should have detailed documentation of root cause analysis, including date stamps and measurement of the actual cost and schedule impact to ensure the impacted contractors are properly compensated.
Boundary of Certification (BOC)
The Boundary of Certification separates phase 3 (Build) from phase 4 (Operate). It is the point of commissioning and handover. RFI changes that occur near the BOC not only have a significant cost impact, they are also likely to produce legal ramifications if the changes delay the opening of the project.
With IPD, last-stage design issues are triaged and the RFI is used as an effective tool to manage necessary changes to the permitted design documents. But on Hard Bid projects, late stage RFIs are treated as bargaining chips in a three-way standoff between the project Owner and Designer of Record.
The power of RFI metrics for project health
New industry metrics like “Phase of RFI Initiation” or “Ball in Court Duration” can be simple but substantial ways of measuring RFI health on a project. When RFIs are presented early in design coordination, and responded quickly through the use of BIM and other automated detection tools, the overall project timeline and budget can be drastically reduced. But to accomplish this, project teams must allocate a budget to account for the increase in Tier 1 and Tier 2 RFIs that will be initiated in Phase 2.
Convincing the project owner to invest early without a guarantee of downstream benefit takes a lot of trust. The best way to build this trust is through transparency.
Do you Trust Your Lean Team Members? Read more in my 3-part series about trust in construction on this blog.
Further reading
Do you Trust Your Lean Team Members?
Improving RFI Efficiency & Insights through a Common Data Exchange
Get Decisions that Stick in Design and Construction
You Cannot Speak of the Ocean to a Well Frog
Nathan Wood, Founder and Chief Enabling Officer of SpectrumAEC, is an innovation thought leader across the Architecture, Engineering, and Construction (AEC) industry. Nathan’s experience with Virtual Design and Construction (VDC), Lean process improvement, and Integrated Project Delivery (IPD) has led him to realize how proven technology solutions can too often result in adoption failure and lost ROI. Nathan blends Emotional Intelligence (EQ) with Design Thinking strategy to help teams overcome adoption barriers through collaborative debate and mutual respect for different perspectives.
Outside of SpectrumAEC, Nathan continues to support industry progress through speaking engagements, industry research publications, and as President of the Construction Progress Coalition.