It’s no secret that large-scale building projects have become more and more complex over the years with numerous design disciplines and contractors involved. As a consequence, the need for collaboration and teamwork has increased substantially. More and more teams realize the value of Lean Construction and Integrated Project Delivery (IPD) and utilize these methodologies for their projects.
Let’s look at implementing Co-Location and Lean Principles on a sample project.
The scope of the project
The sample project in Northern California is a three-story, approximately 100,000 square feet expansion of an existing hospital for emergency services and critical care.
- Level 1: 27 new Emergency Department treatment bays and 7 new triage rooms.
- Level 2: 3 new catheterization laboratories (cath labs), a 12-bed Intensive Care Unit (ICU), and shell space for one future cath lab and four future Operating Rooms.
- Level 3: a 12-bed ICU units and shell space for a future 12-bed ICU unit for a total of 36 additional ICU beds.
- Renovations: there are approximately 10,000 square feet of various renovations that range from the Central Utility Plant to food service in the main hospital.
Four key factors for design success
For the successful completion of the complicated project, four key factors stood out:
- Proximity
- Process
- People
- Culture
Let’s have a closer look at each of them:
Proximity
The 7,000 square foot Co-Location Trailer (CoLo) is situated on the hospital campus and functions as the design and construction administration hub for the project. The team spends 80 percent of their time on site and 20 percent connected to their respective home offices. The CoLo provides the team of architects, designers, engineers, owners, inspectors, general contractors and trade partners a central space to collaborate. The space has cubicles for all team members with no private offices. Small conference rooms surround the work area for break out meetings and a large “Big Room” is located next to the work area for planning sessions and meetings with up to 70 people.
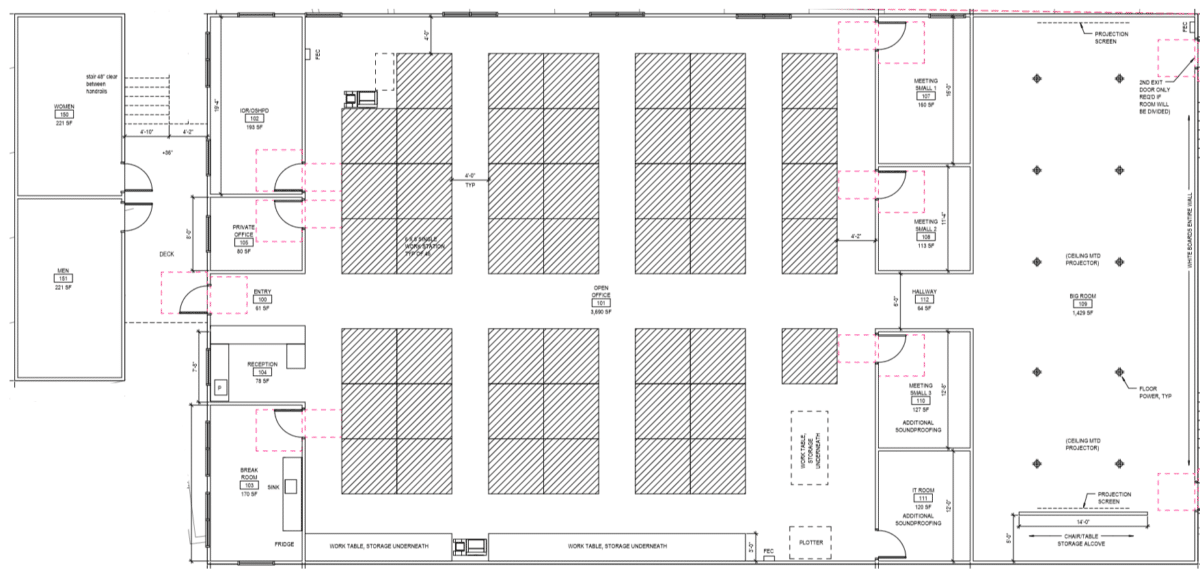

Floor Plan of the project Co-Location space with cubicles in an open work area surrounded by small meeting rooms, a break room and a large Big Room collaboration space on the right side of the plan.

When people work together in a cross-functional team, every participant has a stake in the collective success of the project. We view this as the formation of a temporary organization formed for the delivery of the project. The CoLo also serves the owner in terms of convenience for user meetings, mock-ups and milestone design sign-offs.
The proximity of the CoLo to the project site also allows for going to the Gemba (Japanese term for where the work is done, i.e. the existing hospital and the construction site), the place where the work actually occurs. This is essential in gaining design confidence whether it be seeing the current state of the renovation scopes or more deeply understanding the user requirements for the expansion.
Process
The project team is adept at using tried and true lean tools, such as Building Information Modeling (BIM), Choosing By Advantages (CBA), A3's and Pull Planning.
One of the processes to highlight in the project is mock-ups. Early in the detailed design phase the design team leveraged vacant space on campus to construct full-scale cardboard mock-ups of key spaces for review with the end users. This allowed us to move some of the actual medical equipment into the mock-up space to feel the space beyond a typical scaled drawing. We then assessed the functionality by running various patient care scenarios to test the flow of patients, staff and materials in and out of the spaces. The process had a profound influence not only on the final design but also on the end user buy-in.
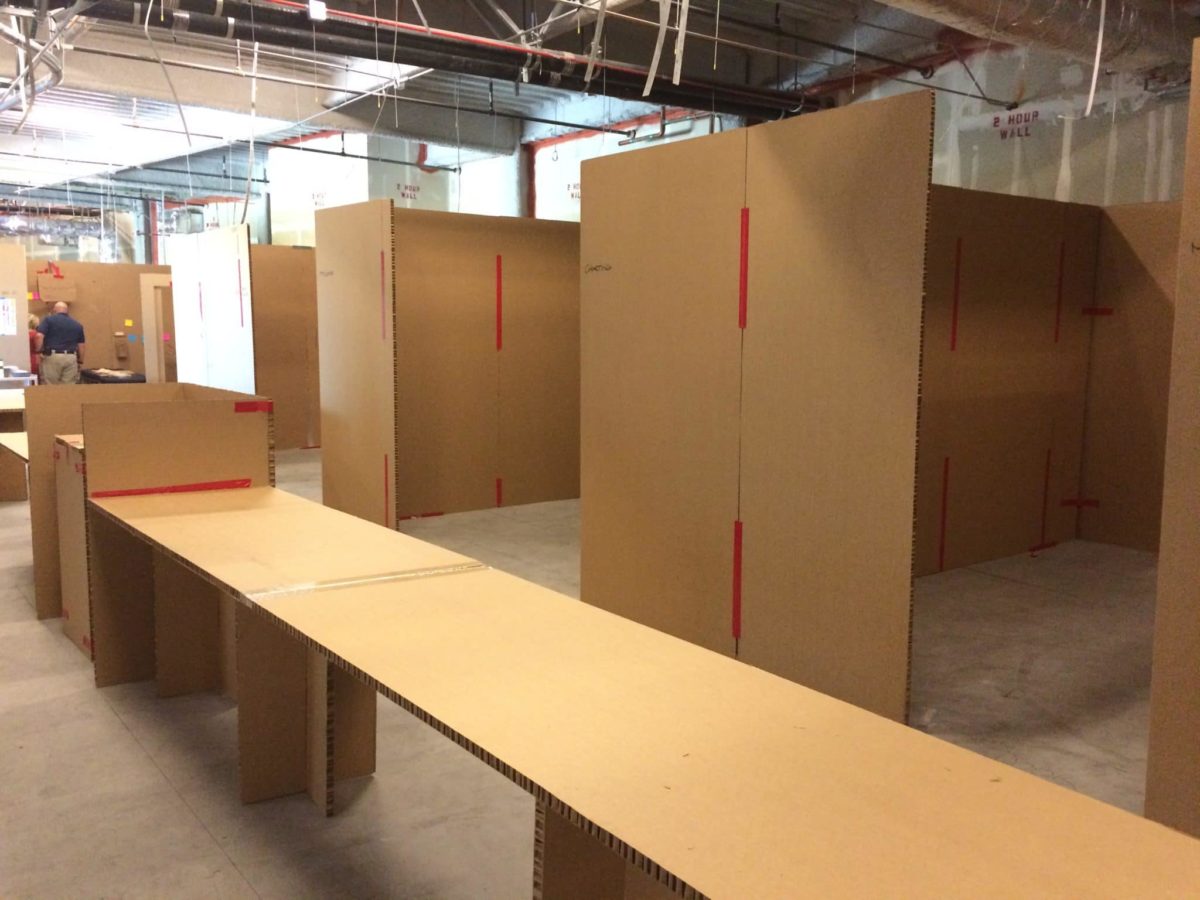
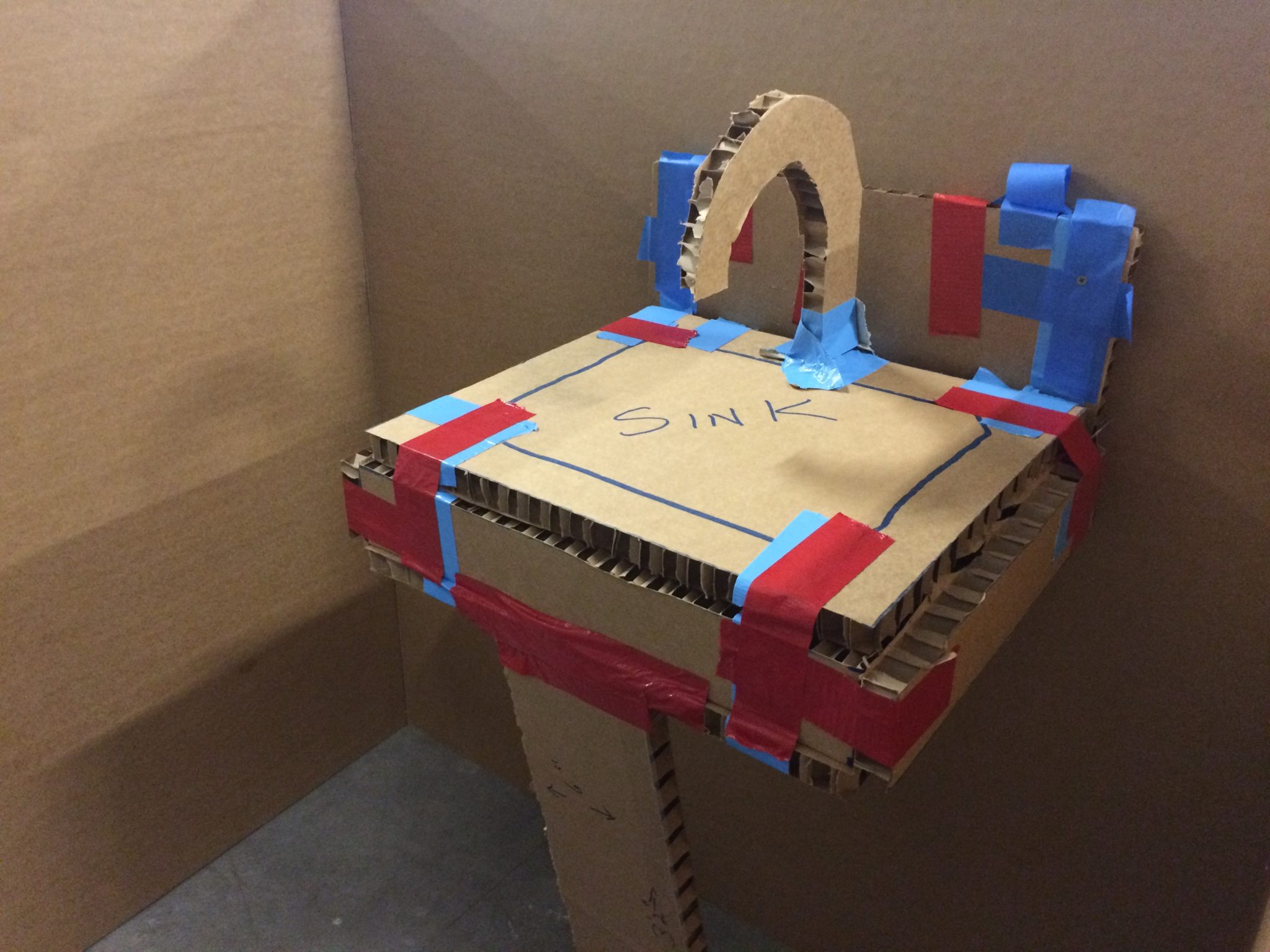
Beyond the mock-ups, the design team used Virtual Reality (VR) to fill in the blanks that the mock-ups couldn’t provide. The users then returned to the CoLo for VR design updates. Moving forward into the post approval/construction administration phase, many processes that we developed support the design work and design flow.
The project team acknowledges this best practice and is open for continuous improvement. One example would be our Friday all-hands meeting to review the six-week construction process ahead. With the understanding of what’s coming, the design team can prioritize resolution to outstanding items and pending design change documentation that supports the construction flow.
People
Casey Stengel, famed manager of the 1950’s New York Yankees, once said, “Finding good players is easy. Getting them to play as a team is another story.” This is as true in baseball as it is in a Lean IPD project. The most valuable resource you have on your project is your people. Our goal from the beginning was to have a highly functioning team. The CoLo is the incubator of that high functioning team. Whether a seasoned professional of 20+ years or a recent graduate starting their first job as a project engineer, the collective efforts of all and not any individual are what make the project successful.
We have had a saying at the CoLo that “we can change the person or we can change the person.” On a rare occasion we have done that! More often than not, however, in the interest of the project and out of a profound respect for people, we would propose to coach that person. For example, instead of saying “no” to a proposal for change we would suggest a “yes, if.” It is that respect for people that is the foundation for trust. And trust is what everything else is built on and what we measure.
"The data on the right shows the result of the survey in December 2016 and which areas need improvement. We focused on the areas of improvement reinforcing behaviors that are lacking. A year later, in December 2017, we ran the survey again. As the results show, we achieved improvement, but we are still working on areas around accountability."
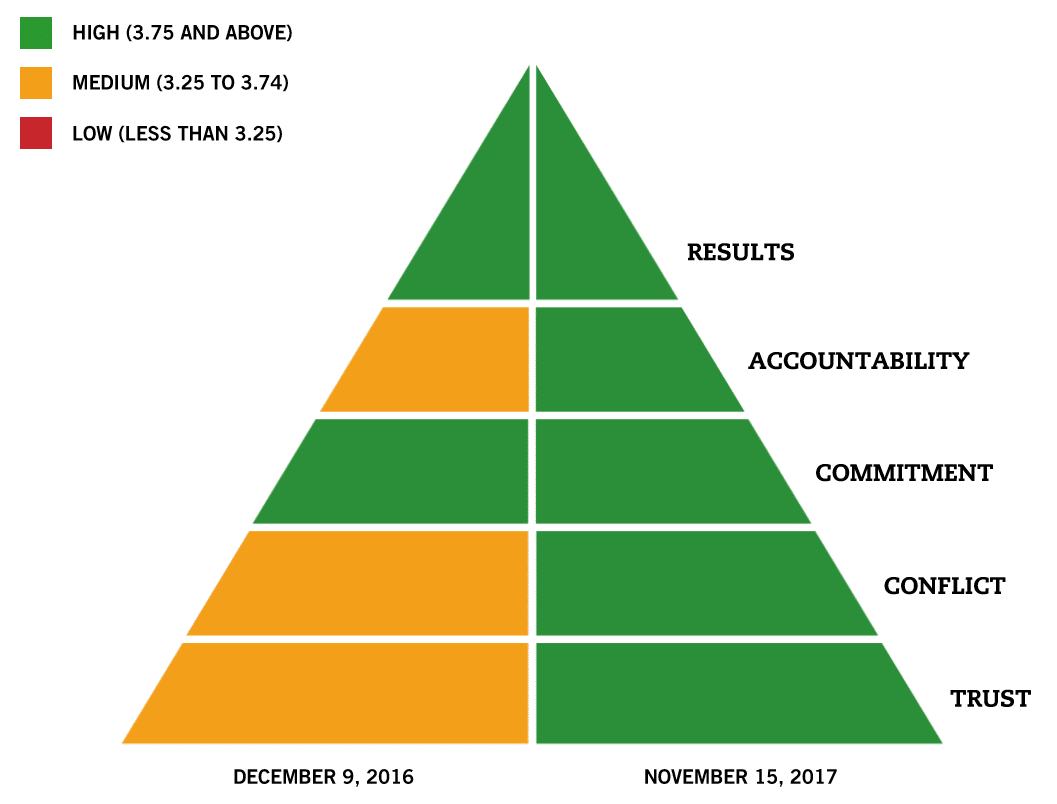
Culture
If people are the parts that comprise the machine of the CoLo, then culture is the grease that keeps it moving. A group of professionals motivated and focused on a singular goal creates a powerful movement. Yes, contracts and profit margins can be a motivation, but taking out the contract is typically a sign that it’s already too late. If a team is operating in a sound culture, profit will most likely be the outcome.
In the first days of the project, the core group assembled to discuss governance, how often which groups would meet, etc. After we had scheduled all the Owner Architect Contractor (OAC) meetings, cluster groups and senior executive team meetings, I asked the question, “When is our all-hands lunch?” So now, since the inception of the CoLo, we have what is known as the First Friday Fandango! This monthly gathering begins with introductions (name and role on the project) and an ice breaker question. We share project information, celebrate milestones and a new ‘Coloian of the Month’ is inaugurated.
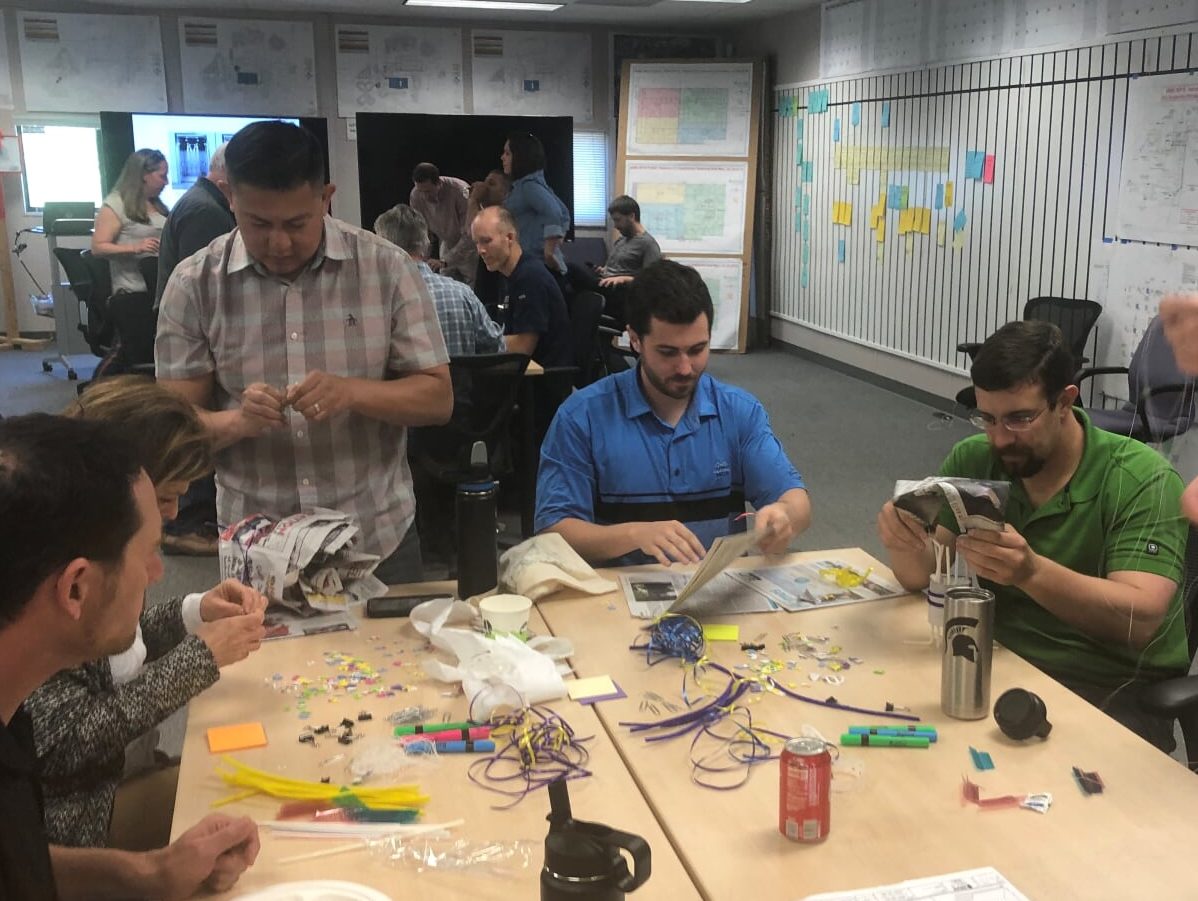
Egg Drop Team Building
You have 15 minutes to use the supplies provided to build a contraption around your team's egg that will keep the egg from breaking when dropped. Once time is up, it will be dropped to see which eggs survive the Eggpocalypse.
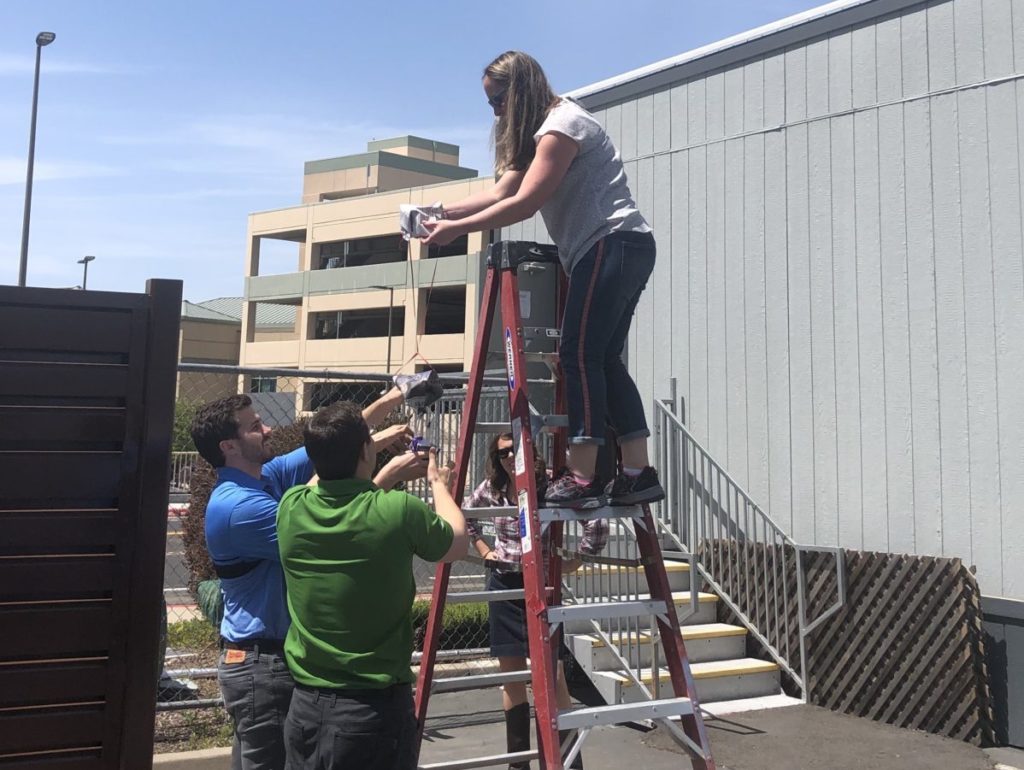
This peer to peer recognition celebrates the folks who are showing exceptional effort on the project. The lunch closes with a team-building exercise chaired by the rotating hosts. In addition to the First Friday Fandango, the team has been together for outings ranging from Top Golf to go-kart racing all in the spirit of fostering and maintaining that culture.
Conclusion
More and more owners are looking to deliver projects in a more lean and integrated fashion due to an increasing body of empirical data to support the project successes. To reap the maximum benefit of lean projects, not only do you need the right tools but also the appropriate culture. Without it, project teams often fail to reach their full potential. Other options are team development training from The Lean Construction Institute (LCI) or engaging a lean coach.
Clients that are seeing the biggest returns are moving “all in” with team development that leverages tools with a continuous improvement mindset in a co-located situation.
Denis J. Stroup is a Healthcare Principal & Practice Group Leader with HGA in their Sacramento office. Denis has 28 years of experience focusing on lean integrated project delivery and acute healthcare design. He is a core group member of the Lean Construction Institute (LCI) NorCal Community of Practice and Co-Chair of training. Denis has a passion for building and sustaining a culture that fosters a highly collaborative environment where people do their best work.