The Pavilion is one of the largest hospital projects in the United States and the largest capital project in the University of Pennsylvania's history. The 1.5-million-square-feet building was finished after five years of construction in October 2021 and houses 504 private patient rooms and 47 operating rooms on 17 floors. It was lean IPD that enabled this visionary hub for medical treatment and science to open and bring patient care at the Hospital of the University of Pennsylvania (HUP) to new levels.
Located in West Philadelphia, the Pavilion sits across the street from HUP’s existing inpatient facilities and adjacent to the Perelman Center for Advanced Medicine (its outpatient center). Bridges and a tunnel connect all three facilities.
What’s unique about this project is its design around patient care. The goal of the owner, the University of Pennsylvania Health System (Penn Medicine), was to make patients feel welcome, empowered and comfortable when entering the Pavilion, providing a more hotel-like experience than traditional hospitals.
Design-thinking with the patient’s experience at the center of everything that happens in the Pavilion has transformed the way patient care is delivered in a collaborative way. For example, all patient rooms have large in-wall monitors for both clinical and leisure uses, including sharing medical data with the patient. Patient data from the operating theatre can be sent in real-time to the computers of world-leading scientists to provide expert assistance during the same hospital stay. Collaboration, Innovation and technology pave the way for both the treatments of today and the medical advances of tomorrow.
Collaboration meets innovation and technology
It was the collaboration of Penn Medicine's own clinical experts with architects, engineers and construction professionals who specialize in healthcare that created positive change and made this innovative approach to healthcare possible. The Pavilion features progressive clinical spaces that meet the clinicians' and the patients' needs alike.
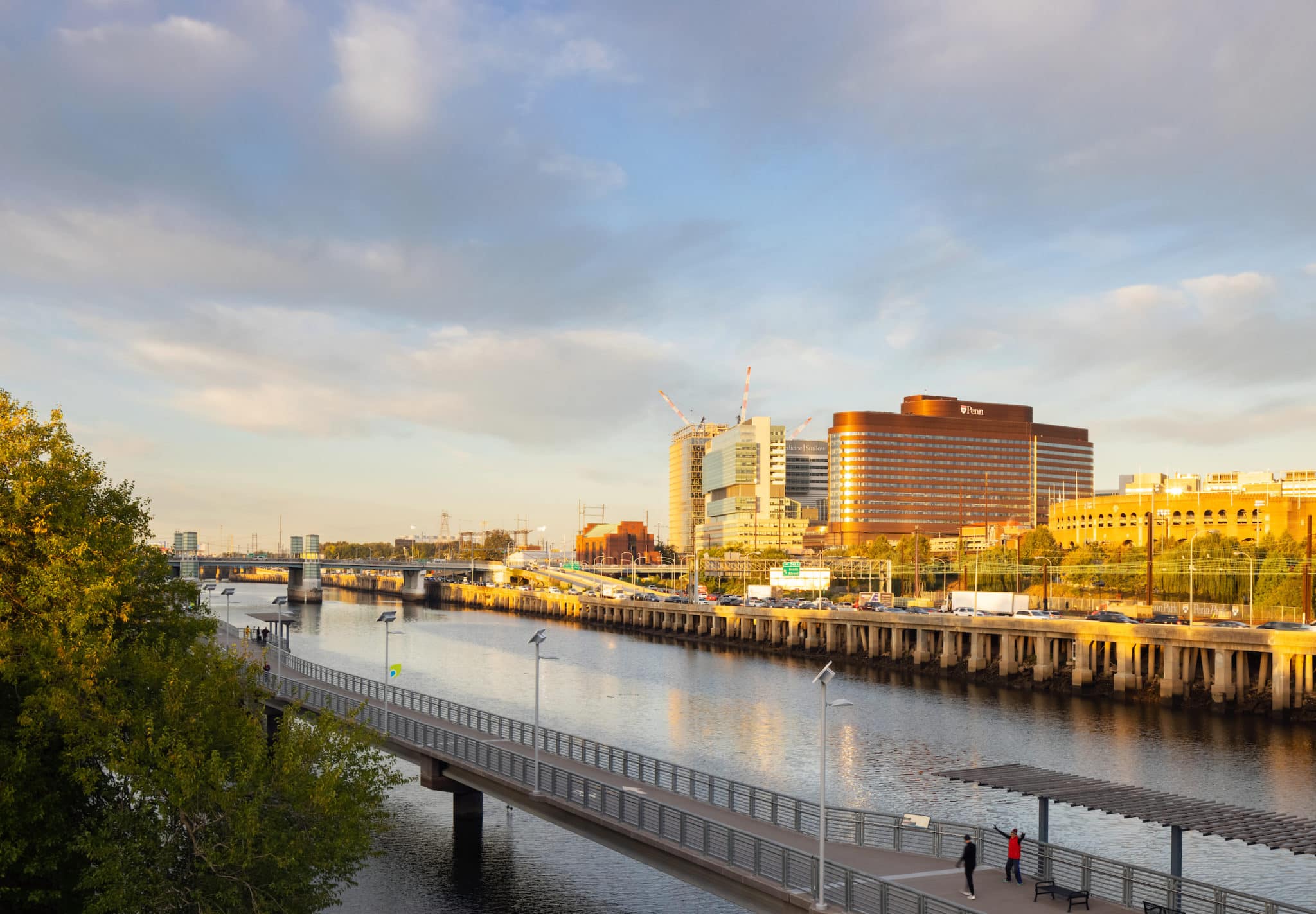
Images: Penn Medicine
Project at a Glance
Building Type: In-patient facility
Project Type: New construction
Location: Philadelphia, PA
Building Size: 1.525MSF
Budget: $1.6B
Schedule: 36 months Design, 60 months construction; construction started 18 months into design
Owner: University of Pennsylvania Health System (Penn Medicine)
Architect: HDR & Foster+Partners
Contractor: LF Driscoll/Balfour Beatty JV
Project Start: March 2015
Completion: October 2021
The Challenges
Almost all of our previous projects utilized an Owner-Architect Agreement for design and Owner-CM (Construction Management) Agreement for preconstruction and construction. The CM agreements were based on a GMP (Guaranteed Maximum Price).
These were some of the frustrations we faced:
- Although we typically had good collaboration between the designers and contractors, there would inevitably be a bit of finger-pointing when issues arose that required adjustment to the design and/or construction, for example: ‘That’s not what was drawn’ or ‘You should have assumed something for that’.
- Change Orders happened for simple and relatively inconsequential things: ‘Do I really have to review, discuss, negotiate a $5,000 change order for …?’
- Haggling over Change Order pricing to get to the true value–and often never really getting to the actual costs.
- Trying to solve an issue–whether design or construction–and getting half-hearted collaboration from one of the team members.
An internal challenge we had to overcome, prior to project initiation, was the resistance from Legal and Risk Management to make the change to a new contracting methodology. Only when Lean and IPD became a topic at more and more industry conferences during 2010 to 2014, and people heard from their peers about its potential, did they started to sense that there is something better out there than what we had been doing. IPD just sounded like a much better way to approach large capital projects.
The Solution
From the construction perspective, some of our teams had begun using a few lean ideas and processes, but not in a focused way, and it was becoming apparent that we needed to help push that along by selecting CMs that were truly incorporating lean practices into their planning and execution. With respect to IPD, this truly felt like a better way to design and build a project; a contractual methodology that could foster and strengthen true team collaboration.
Once we had made the decision to go with IPD, things started to flow from there. A few of our CMs had already started implementing some Lean practices, so it was easy to work with them to look for more lean ideas. And more teams quickly followed. Getting buy-in and full commitment from some of the subcontractors and labor was more difficult and has taken longer.
True partnering is the recipe for success
IPD has definitely helped us overcome many of the challenges of the more traditional design and construction contracts. The true IFOA (Integrated Form of Agreement), with numerous partners, has helped eliminate or dramatically reduce those issues. We are very clear during the team selection phase that all parties are to be true partners; it is to be project-first and company-second for all participants. The realization that:
1) You can’t lose money, but
2) Your profit is at risk
really gets the team working together to create the project and collaboratively solve issues as they arise.
Quick problem-solving to maintain schedule
My favorite part of our Lean IPD journey is watching people and organizations change the way they function and operate with others. It is very rewarding when someone who’s been in the business for 20 and 30+ years says:
‘I did not think this would work, but I was wrong’ or
‘Why haven’t we been doing it this way before?’
I also love the way Lean IPD can solve problems in a very short time. We’ve had numerous occasions where an unexpected situation arose, and it needed to be solved quickly to maintain schedule. The right people from different firms (designer, engineer, subcontractor, CM, Owner) got together and worked through alternatives to settle on the best solution for the project, not one specific member of the team proposing the best solution for them and their company.
Results
I believe that using IPD and Lean has produced projects with more program for the dollars than traditional contracting and performance methodologies. Overall, Lean produces safer, cleaner, more efficient, cost effective projects. And that means a better project outcome for all involved parties.
The Pavilion finished on schedule despite Covid interruptions, and the profit pool was maintained.
Watch A Beacon of Hope: Penn Medicine's New Pavilion to get more insights into the future of medicine.
Related articles
New Research Testifies IPD Project Success in Canada
New IPD Case Study in Canada
Collaboration, Communication, and Culture Create Succes for the Canada Games Aquatic Center
IPD Makes Dream Come True for Two Canadian Schools
Steve Greulich is Associate Vice President, Real Estate Design & Construction at the University of Pennsylvania Health System (Penn Medicine). For the past 7 years, Steve led the Integrated Project Delivery (IPD) team on the Pavilion project at the Hospital of the University of Pennsylvania. Steve has 40 years of experience in the design and construction industry, both as an Owner and Builder. He received a Bachelor of Architectural Engineering degree from Penn State University.
Steve has been with Penn Medicine since October 2006 and has had oversight of many capital construction projects in the past 16 years, ranging from small renovation projects to the $1.6B Pavilion project to campus-wide master planning efforts. Prior to Penn Medicine, Steve worked for large CMs in the Philadelphia and Washington, DC areas as well as for SAP, managing all aspects of a new headquarters project.