What does Takt Planning & Scheduling have to do with Covid-19?
Takt is a German word that refers to the rhythm or the beat of the music.
Takt Planning & Scheduling is a method to structure work around a set pace and could, therefore, be one of the most important construction practices to keep both your workers and your bottom line healthy in times of Covid-19.
Why? Because Takt Planning & Scheduling treats ‘space’ as a critical constraint.
On an automobile assembly line, cars move down the line to workers who have a designated space to do their job. Similarly, with Takt Planning & Scheduling, construction workers have a designated space to do their job.
So the main difference is that instead of the work coming to the worker, the worker goes to the work for a specified time or Takt.
Time and space are linked
A significant benefit in these times of physical distancing is that a Takt Plan & Schedule focuses on providing sufficient space for workers to do their tasks. Once workers complete their jobs, they do not proceed to the next area until the start of the next Takt. A little buffer ensures everyone is finished before the start of the next time unit. As a result, the job progresses at a predictable pace.
This is not a new idea. After World War II, many of the large suburbs were built using this method with great success. Productivity, as well as cost and schedule certainty, went way up. It also reduced training time and enabled workers to master a specific skill set.
BMW sets benchmark with factory in Brazil
BMW is a leader in Takt Planning & Scheduling. It should be no surprise that a car manufacturer with years of experience applying Lean principles and practices to manufacturing was now successfully applying them to construction. A great example is the plant BMW built in Brazil to assemble the all-electric i3. This assembly plant was built in half the time and at half the cost of similar projects.
The sketch below shows the overall Takt Plan for the BMW Assembly Plant in Araquari, Brazil. It’s astonishing how powerful and simple it is.
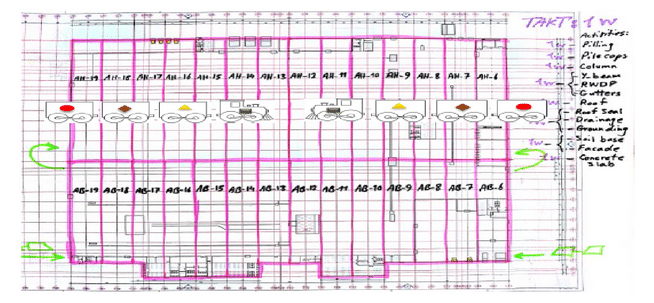
The Takt time for building this plant was one week because two trains of workers started from the outside and worked their way to the middle. It’s worth noting that this simple sketch replaced multiple pages of a typical construction schedule.
Image source: Three-Level Method of Takt Planning and Control
The mantra to follow is just as simple:
Takt if you can,
Pull if you can’t,
Push as a last resort.
Create flow, eliminate waste
The goal of Takt planning is to create a reliable plan and workflow with the input of the entire team to eliminate waste as work progresses through the construction project with a predictable rhythm.
And with the need for physical distancing, the value from Takt Planning & Scheduling has never been greater.
Further Reading
Three Level Method of Takt Planning and Takt Control - A new approach for designing production systems in construction
Dissertation: Takt Time Planning as a Work Structuring Method to Improve Construction Workflow
An Introduction to Takt Time Planning
Takt Time Planning - When the Train Falls off the Track
Mike Staun was the Engineering AD for Global Capital Management at Procter & Gamble (P&G) until his retirement on July 1, 2019. To gain a competitive advantage, Mike focused on achieving greater value from P&G’s annual $3.5b CapEx by moving to Lean IPD as its preferred project delivery method. In his 36 years with P&G, Mike had numerous engineering and manufacturing assignments in the company’s Beauty, Health Care, and Fabric & Home Care businesses. Mike currently serves as chair of the Lean Construction Institute (LCI) Board of Directors.