When people hear the word research, they often think of research in science or medicine that seeks new solutions to known problems by building on studies that came before. It's expected that new research builds upon previous findings and does not repeat them.
To give you an example from the medical field: If you have a heart condition and consult your doctor, he/she will recommend a treatment plan based on your health history, your demographics, and your symptoms. Your doctor will recommend a solution that is going to give you a better chance of success than another one. He/she is able to make a suggestion based on past research and to forecast that you are more likely to have success with one course of treatment than with another.
In summary: no one expects a doctor to guarantee that one course of treatment is going to be better than another one, but we expect that a doctor can tell us which treatment is more likely to be successful based on other people who have been in similar situations and based on the studies to date. No one wants to hear their doctor say: ‘Trust me, this treatment is the one I always use because I just have a gut feeling it's better than the others.’
Unfortunately, research in the building industry does not give its practitioners the ability to take the former path, which leaves us too often in the “trust me” mode. There are many reasons why research doesn’t support our expertise. I will focus on two of them in this article.
There is no formal research structure in the building industry
When a building client comes to a contractor or a designer, they can't expect to hear: ‘Given your choice of these four sites, I would choose this site because based on baseline industry standards the percentage likelihood of these things increases or decreases.’ The contractor or designer can’t even say: ‘If you choose to go with us and use IPD, you will get this much better of a product, much faster, or this much more reliable of an outcome than if you go with the exact same site project budget with a team that doesn't use Lean IPD.’
In the building industry, we can market our expertise, but we can’t offer evidence or baseline improvements shown over a large enough sample size to back up our claims.
One of the fundamental differences compared to many other fields is that in the building industry, we don't have a formal research structure. What we have is a lot of people doing work that they consider research, but a lot of it is intended to stay proprietary, not shared. This makes sense if you are trying to build your reputation for expertise and to position yourself in the market. But it also means that you don't share findings for others to verify and build upon, which limits the industry’s ability to advance as a whole.
The second difference is that in the construction industry, it's very difficult - if not impossible - to do controlled experiments because we usually don’t build two exact same buildings. Even if they are identical in their configuration, there will always be differences, for example, site conditions vary the foundation conditions, the timing of the project may vary the labor economic conditions.
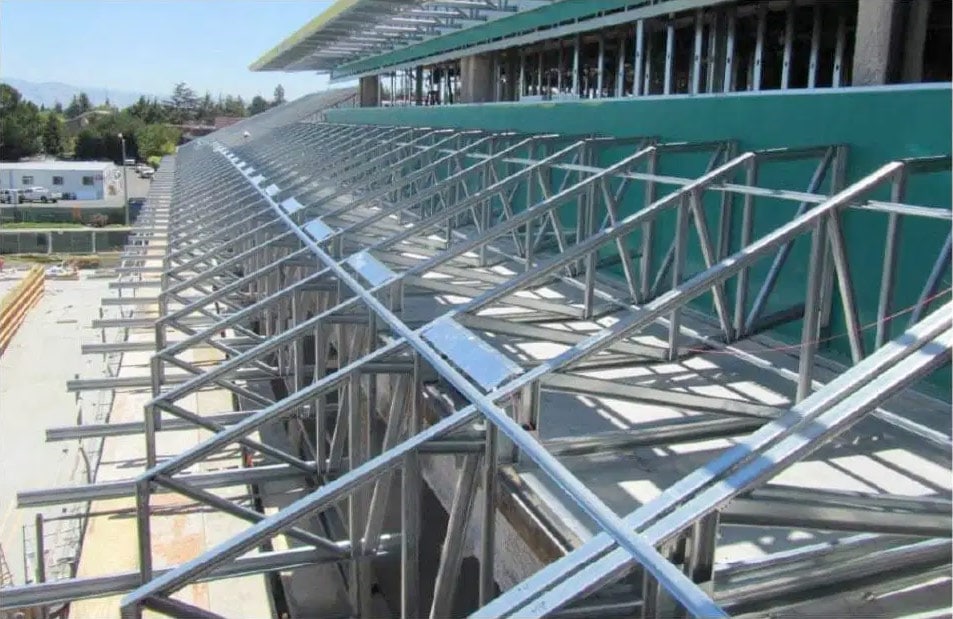
We need major shifts in the building industry
When you look at the design and construction process of a building, expanding to its use over time, the number of variables is just so enormous that we struggle to even begin to define what an experimental scientist would call rigorous research.
What we are left with is episodic. For example, a lot of construction companies track construction costs to project costs for their clients as reliably as they can. But they don't share this information broadly because it's proprietary and gives them the market advantage. And they each develop their own set of cost measures and their own methodology for setting those metrics. Even if we could get everyone to share, we are unable to compare data in an apples-to-apples way. As a result, we don’t get any better as an industry at becoming more accurate and reliable when setting cost and schedule goals.
Then, there are industry groups such as GSA (General Services Administration), which is the Federal Government’s largest landlord, and AIA, the American Institute of Architects, who have done some research efforts around baseline data. However, they are more focused on building performance than on the form of contract or method of delivery used. So you only get a partial picture, and, we don’t see how success in building performance is tied to how the team sets their cost and schedules goals. And lastly, we have to acknowledge that in our industry, it's rare to find people who trained in research.
What I found is that there’s too much variability in the questions that one would expect should drive our industry:
What should I budget for time, and what should I budget for money, given certain expectations of quality, performance or complexity?
And because we don't have a really reliable sense of what's a baseline for time and money, we can't say, if we use IPD, how much better than baseline we are getting for those measures or for better quality. Which is very frustrating!
From studying drawing techniques to researching teamwork
Back in the days when BIM was very new, I was working as a researcher studying drawing techniques and ways that architects use notations and other things to model and present and communicate their design ideas through drawings. I was looking at what they would need to convert their idea into a representation that someone can put a price on and build it.
The transformative potential of BIM was to essentially rehearse construction, so you could see where there was an error or an omission, a missing piece of information. And you could also run diagnostics around seeing places, for example, where the plumbing would be interfering with the ventilation systems or whether there was a problem with the sequence of assembly. The problem could then be resolved in the model before it would become a problem in the field.
This idea of rehearsing construction and improving the drawings was something that I began to document as a researcher in terms of how it changed the way architects communicated. I also looked at the legal implications of who owns or is responsible for the information in the BIM, what information we were accepting from manufacturers and how the model was being used to actually generate computer-aided design or manufacturing. All these were new questions compared to how architects’ drawings had been used in the past. BIM was interesting to study because it seemed to allow architects to play a different role in the team and for the team to work differently.
After many years of working as an architect in the field and from studying the history of construction, I was frustrated with recurring problems created by inefficiencies, mistakes and delays, which have plagued the industry since medieval times. Some inefficiencies are acceptable because they give you more time to test things out. Mistakes, omissions, and delays in feedback loops, however, are wasted energy. It was pretty frustrating to see that a project that had the potential to invest into higher quality design or construction had to be reduced in scope to make up for mistakes or unanticipated problems.
So I started researching to find projects where teams were able to achieve really challenging goals or more innovative ways of reaching conventional goals. I used various techniques to look into the way teams work as well as the way they were documenting and the way that were passing information or owning information.
What I found was that the more teams were integrated, the easier it was for them to use contracts, tools, and processes to reach their goals.
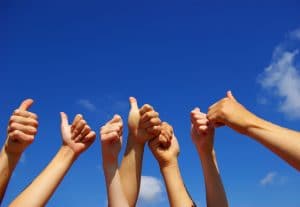
Psychological safety is key to success
From the work I have done in cooperation with Lean experts, such as Markku Allison, I found that there is a causal relationship between success in meeting challenging goals and being a more integrated team.
We looked at a set of high-performing buildings and high-performing building teams, and we have been able to extract metrics that we call qualitative or “soft”, such as
- Did the team feel they had clear goals?
- What did they do in their early planning?
- How did they decide which lean tools to use?
- How did they learn which lean tools are most effective for them?
- How did they use BIM?
- If it was an IPD contract, who was involved early, who was involved later?
There have only been a few findings that we have been able to confirm with reliability, and all of them have to do with Psychological Safety, which is a term that comes from Business School research and Social Sciences. Amy Edmondson is known for her groundbreaking work on psychological safety in the workplace, and I recommend watching her TED Talk Building a Psychological Safe Workplace.
In our research work, we set metrics for a team to score a certain numerical or qualitative score for trust and respect, for example. And we found evidence that there is causation between trust, respect, accountability, and clear roles in a team. They are the ingredients that lead to team and project success.
As a consequence, we were able to to prove that it was the psychological safety and the ability to speak up and say the dumb thing, ask the question that you think has an obvious answer, trust that your team is not going to make fun of you, that you're actually going to get heard and be respected. A team with such a culture is able to question assumptions and actually reach some innovation. They tap into people’s expertise and bring forward the differences that might be coming from very different backgrounds, skills, and training.
For example, let’s say the site superintendent, the designer and the mechanical engineer were able to ask questions of each other that might seem really obvious but actually lead to innovation, to cost savings, and to different ways of doing things. The research we do uses methods common in social sciences, and we are mostly dealing with qualitative or the softer kind of human interaction aspects of how the team works together as opposed to the harder metrics. However, there is a quantitative backing based on numerical scores from questionnaires surveys.
In the end, it's about how reliable is the team in meeting the schedule, quality, and budget goals of the project?
Setting good goals is crucial
All of our work depends on the owner being able to set reliable goals for project schedule quality and budget. If you are an owner, for example, and you are subject to huge penalties for being over budget, you would probably set really generous budgets, or you would have very conservative scopes because you really don't want to be over budget, right?
As a result, your budgets might be much higher than you think you really need so when the project is done, you can say ‘we came in on or under our budget’.
It's similar to airlines wanting to claim their flights are 100% on time. To be able to say that, they will schedule a flight time of 1 hour and 20 minutes when the flight actually only takes an hour. So if the plane takes an hour to get to its destination, they land “early”. And if they are delayed and the flight takes an hour and 20 minutes, they're “on time”. It's all a matter of setting expectations.
What this example illustrates is that you can pad a budget and a schedule by reducing your scope or by adding more time than you think you're going to need.
But think of all the waste in this approach. If you had a reliable budget and schedule, you could use money and time to invest in increasing quality or performance instead of holding it as a contingency fund just in case you need it.
Currently our industry metrics of being on time and on budget are not only unreliable, they are not helping us improve the built environment or to get better as an industry.
If we knew what is an on-time budget for a construction of this size in this market sector in this economic condition on a site like this, etc., then we could talk about what it takes to improve on the baseline
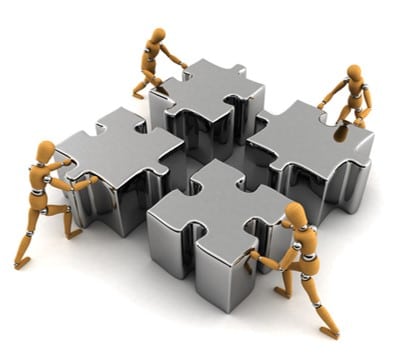
The majority of projects are over time and over budget
What we know is that most projects are over time and over budget, or both. Some studies show figures as high as 70%, and the question I have is:
Who is setting those budgets and schedules?
And, are those projects really missing their targets, or are the targets set on unrealistic expectations?
On the other hand, we see so many Lean and IPD projects being on time and on budget, it is pretty clear there is a pattern. What’s the cause of that pattern? What we found in all the teams that we have studied is that Lean IPD teams have a better sense of the budget and schedule because of the validation process. That’s when teams work back and forth between their target budget and target schedule.
During this process, they ask:
Can we meet the expected scope within this budget and schedule?
They feedback to the owner what they can do or what they need to adjust to meet the project goals. In other words, they start the project with a much better understanding and they have metrics to hold themselves to that promise.
This mutual understanding is all developed within one team, which is doing the same things that everyone else in the market does, except they're doing it with slightly different goals, unified goals, and they have a slightly different way of holding themselves to their budget.
In the IPD world, team members share information about their base costs, direct costs, overhead, and profit. They are honest and transparent about it, which goes all the way back to establishing mutual trust, respect, and accountability – the basis for psychological safety.
In summary
The type of quantitative research we have in science or medicine is not going to be powerful in the building industry until we shift towards a formal research structure, which will require a lot of coordination. But until then, we have effective qualitative research that we can do, and that research can help us align around the shifts that are needed.
In my next article, I will share my latest work in Lean and equitable practice.
More from Renée
5 Myths about IPD and Lean
Why Lean and Diversity are Going to Get you the Best Results
Further reading
Are you Collaborating or Muddling Through your Construction Projects?
IFOA and the Advantages of Bringing People Together Faster
Renée Cheng joined the College of Built Environments as dean on January 1, 2019. Dean Cheng comes from the University of Minnesota where she was a professor, associate dean of research, head of the school of architecture, and directed an innovative graduate program linking research with practice and licensure. Prior to UMN, she taught at the University of Michigan and the University of Arizona. She is a graduate of Harvard’s Graduate School of Design and Harvard College.
A licensed architect, her professional experience includes work for Pei, Cobb, Freed and Partners, and Richard Meier and Partners before founding Cheng-Olson Design. Dean Cheng has been honored twice as one of the top 25 most admired design educators in the United States by DesignIntelligence. She has received numerous honors and awards including the 2017 Lean Construction Institute Faculty Award and was named to the American Institute of Architecture’s College of Fellows in 2017.
Cheng is a leader in the American Institute of Architects (AIA) and advocates for equity in the field of architecture and in the practices related to the built environment. Recently, Cheng led the research effort for the AIA guides for equitable practice in the workplace. Cheng has pioneered research surrounding the intersection of design and emerging technologies, including work on industry adoption of Integrated Project Delivery, Building Information Modeling, and Lean.