Industrialized construction and pre-fabrication are hot topics in the commercial construction industry. If you are involved in an IPD project or are deploying other lean construction practices on your project, such as the Last Planner System, Target Value Design, or flow improvement methods, you have certainly come across the idea. In this article, I want to share five benefits of using prefabrication but also give you some guidance on what to look for to prevent problems that could reduce the positive impacts of deploying pre-fabrication methodologies.
Almost every single project in North America today uses prefabrication. If you import ready-mix concrete to the site, you are getting the mixture prefabricated with concrete rebars, structural steel, mechanical units, doors, windows, and casework fabricated off-site. A portion of what we currently install on site is fabricated and assembled off-site. It’s not a matter of doing it or not, it’s a matter of increasing our volume of work done off-site and applying it to new scopes of work. We have precedents we can follow in our own industry.
A scale of possibilities
As an experiment, look at every single piece of material that crosses the front gate of your job site over the next few weeks. Take a piece of paper, make five columns using the headers below and put a checkmark in one of the columns for every one of those materials.
After a while, you should start to see the distribution unique to your project and what stage of construction it is at. Construction projects are all unique, which is the beauty of our industry, and I estimate that 20 percent are at least prefabricated today.
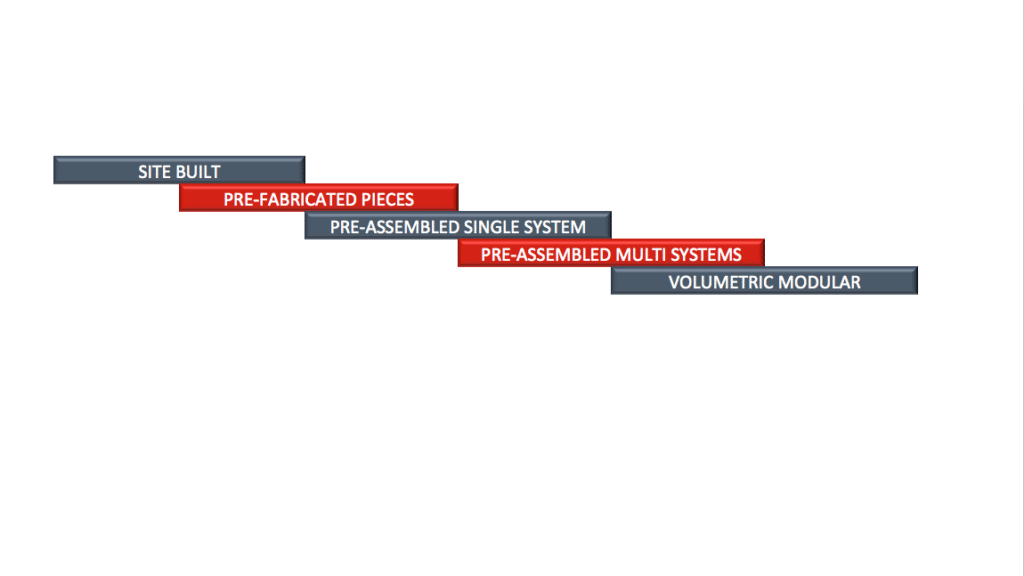
Illustration: Dominic Desmarais
I spent ten years in an integrated volumetric modular construction company. In this model, we did 80 percent of our work above grade in a factory and self-performed about 90 per cent of our design and construction work. We prefabricated parts and pre-assembled systems and put them together in volumetric modules before shipping them to the site with loose parts. I experienced the whole spectrum in several projects. The benefits are multifold and often misunderstood.
Benefit #1: A controlled environment
Operating in a controlled environment offers added labor efficiencies. Most of those come from better working stations, improved work conditions, known locations of work, smaller work footprints, and better equipment and material distribution processes designed to suit the workers. All those factors help reduce the labor component of work primarily, most of which is prep time, some transformation time, some damages, and scrap. The controlled environment itself accounts only for a proportion of the gains in productivity–from my experience it is in the 15-20 percent range–in comparison to traditional site construction.
Benefit #2: Labor efficiency
When repetitions of sub-assemblies invite themselves to a project via its value proposition, first-run studies and associated learning curves will result in labor efficiency. My experience overseeing the financials of repeat and non-repeat modular projects showed me that teams can expect to see a 25-35 percent labor reduction over the fabrication of around 10-12 sub-assemblies of similar nature. The labor component seems to normalize after such production runs. The volume of sub-assemblies to produce for a project, therefore, becomes a great driver in a team’s desire to pursue such practices. True one-off highly customized projects may see fewer returns in this category of efficiency.
Benefit #3: Increased coordination and constructability
From my experience, there is a remarkable difference between the quality of the information provided on manufacturing drawings and “standard” construction drawings. I still wonder how our talented tradespeople can complete their work assignments with such levels of information. I believe drawings made in the AEC industry today are at best 75 percent representative of reality, which means it is impossible for our trade contractor to follow the layout and dimensions depicted to build the project.
The term DFMA (Design for Manufacturing and Assembly) is gaining in popularity. Without the guarantee that things fabricated off-site will fit on site, who would consider spending time and money off-site to have it re-done once delivered?
The picture below shows an area inside a building with both pictures taken in the exact same location. The picture on the left is a design model, and the picture on the right is a trade contractor model. One can understand productivity and prefabrication is not just about increasing the level of details on the design model, it's about modeling for trade assembly. From my experience, 25-35 percent of the improvement in labor efficiency available to projects comes from the increase in the constructability of the model itself, reducing rework and facilitating better workflow amongst trade contractors.
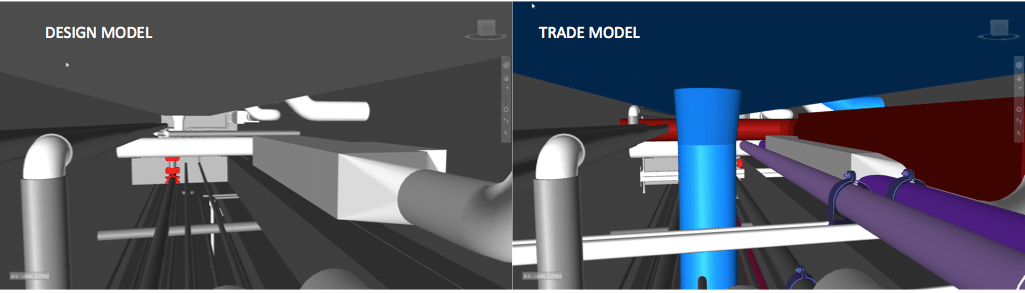
Images: Dominic Desmarais
Benefit #4: Schedule acceleration
Schedule acceleration is another key driver of prefabrication. Depending on the density and type of off-site assembly your project is pursuing, the impact on the “traditional design and construction” process will vary. As a rule of thumb, it is fair to say that the more pre-fabrication you intend on doing, the earlier this decision needs to be included in the process. Prefabrication can shave off anywhere between 0 and 40 percent of your construction schedule. As a project team, it reduces your general management and overhead costs by a proportional amount. Prefabrication can be used to dodge increased costs due to seasonal variations in construction costs and help declutter dense construction areas. The proportion of benefits from schedule acceleration can range from 10 to 30 percent of the total cost improvements available through such methods.
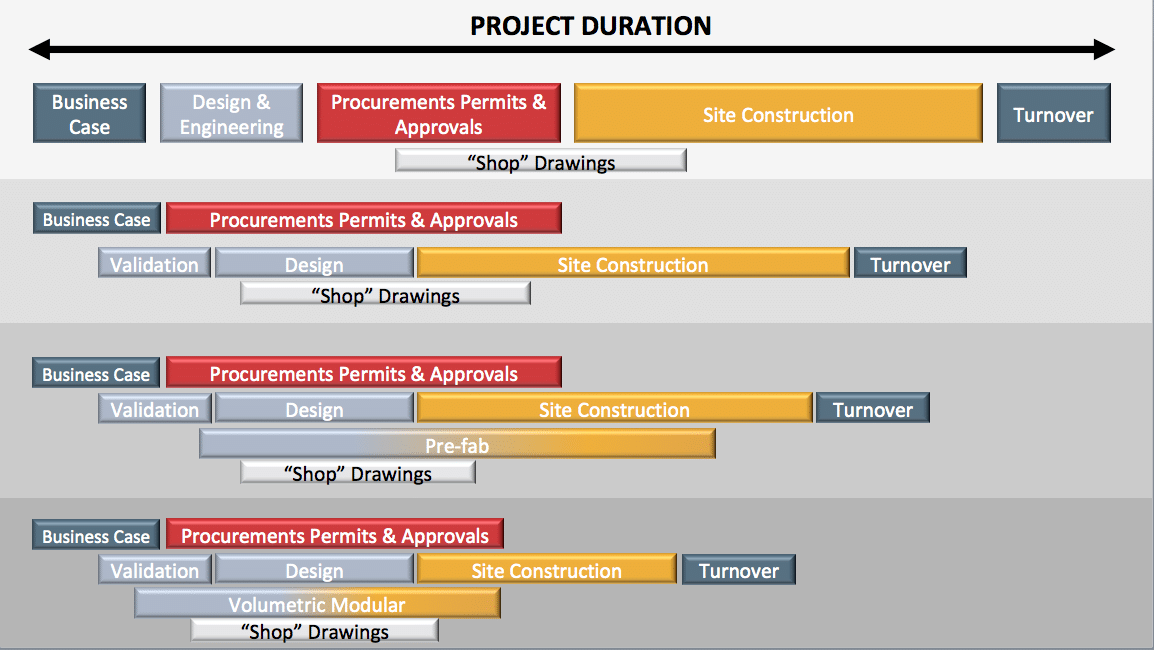
Illustration: Dominic Desmarais
Benefit #5: Automation and robotics
People have a fascination for fancy technology such as fully automated equipment and robotics. Such capital investment has proven useful for many production systems. These technologies primarily displace the variable cost of labor and all the “risks” that come with it into fixed costs that can be owned through property rights. From a business and legal perspective, they are attractive.
In construction, however, we must be careful. There are many indirect costs associated with such technology, in my experience, however, we have not yet reached the threshold for economic benefit. Machines need volume, consistent volume, and repeat volume over several projects, over several years. The timing and matching of supply and demand in our industry is one difficult puzzle to solve, which contributed to the structure of traditional construction as we know it. Local optimization appeared to be a good countermeasure.
Individual companies may elect to pursue such investment in technology, however, based on the current state of the industry, the independence of our trade contractors, the variety in volume and the uniqueness of the project and the volume required to generate enough savings to pass a noticeable portion on to our project owners.
Some specialties will see more benefits than others but I believe it should not be the place to start given the issues we are still having with team synergies, information quality and production control. Many lean manufacturing people recommend automating last.
In summary
Prefabrication and pre-assembly are valuable methods that should be used by the project team to reduce costs, accelerate the schedule, and increase the density of value delivered to customers for the same price. The benefits of these new methods of construction are multifold, and working in a controlled environment is just one of those. Teams wanting to pursue such practices should realize that the first step is to increase the quality of the information provided to trade contractors and ensure constructibility. With better information is it possible to move production off site while still guaranteeing good constructibility. Such improvements can be done together or not, the potential for improvement will however be proportional. Conservative teams can first attempt to deploy pre-fabrication by moving such activities on site but away from the final assembly areas. Such an interim step could give the team a level of confidence and help iron out the bugs before deploying in larger scale and adding logistics complexity to the construction process.
Every project is unique and how far a project team will be able to go with increasing the density of prefabricated work is a function of both the characteristics of the project and the composition of the team. Understanding how prefabrication can benefit the project business case and its value proposition early on can help owners establish a procurement strategy that will be well-suited to realize such benefits.
The benefits of prefabrication are numerous, however, prefabrication, pre-assembly and modular construction also come with new constraints and pitfalls. In the second part of this article, I will dive into the things you need to be aware of and protect against to ensure the gains possible don’t slip between your fingers or worst, vanish and increase your cost of construction.
Feature image: Samuel Regan Asante via Unsplash
Related articles
Project Mountain: Build Better, Faster, and Cheaper
Can Owner Standardization Transform Healthcare Construction?
Who Benefits from Innovation in Design and Construction?
What Every Project Owner Should Know About Intelligent Construction Drawings
Dominic Desmarais P.Eng. is a Canadian Professional Engineer with 20 years of industry experience in deploying lean thinking as a project manager and senior leader in both manufacturing and construction. He has a technical background in industrial engineering and a specialization in the design of production systems. In his work, Dominic has experienced the ups and downs of business cycles in different marketplaces along with various levels of success with the deployment of progressive management practices such as lean management. He participated in the integration of lean thinking in several companies such as a vertically integrated Design-Builder-Owner-Operator, where he became the senior leader of their modular construction operation. He has since been working for general contractors, helping project teams with the deployment of lean thinking and practices such as IPD, TVD and LPS. Dominic’s curiosity and relentless desire to improve business performance makes him a long-term student, intense thinker, and passionate promoter of progressive management practices. He currently lives in Edmonton and travels across North America to support the deployment of lean and IPD for Graham Construction and Engineering.