How is IPD Different From Other Contracting Models?
Integrated Project Delivery sets up a different environment than other delivery models such as lump sum, design/build, and guaranteed maximum price contracts.
One area where this is most evident is in how changes are made after the agreement is signed and the team is delivering the project.
This page examines a case study where implementing major modifications to the building design and construction sequencing resulted in significant cost and schedule savings and how those changes where implemented contractually.
Building Summary and Background.
This example is from a three story ground up development built on top of 2 stories of underground parking.
The parking garage was excavated and then constructed with cast in place concrete using mild steel reinforcement. The top of the parking garage is at grade and consist of a 14 inch thick podium deck with some cast in place structural steel beams. The three story building is composed of structural steel sitting on top of the podium deck.
The overall schedule for the project had the critical path running through placing the concrete podium deck prior to start of structure steel. Due to the size and complexity of the podium, erection of the steel and the subsequent start of the tenant improvement was a 3 month duration on the schedule.
Opportunity: One of the Project Engineers on the project asked the team why the building couldn't be erected on top of the lower level columns, then placing the podium deck around the base of the steel columns once construction of the tenant improvement was underway. This would allow the tenant improvement to start months earlier than the current schedule.
With this simple question, the team went out to study the potential answer and determine how that might be possible.
What Does This Mean for the Building Structure?
- The steel columns in the original plan land on the podium deck.
- In the proposed plan, the podium deck is not there yet, so the columns need to extend down to the concrete columns.
- The steel package increases now that all of the columns are about 18 inches longer.
- The detailing of the rebar at the top of the columns needs to change to accept the steel.
- The rebar also needs to change to allow for placement of the podium deck into the top of the columns and around the steel base plate.
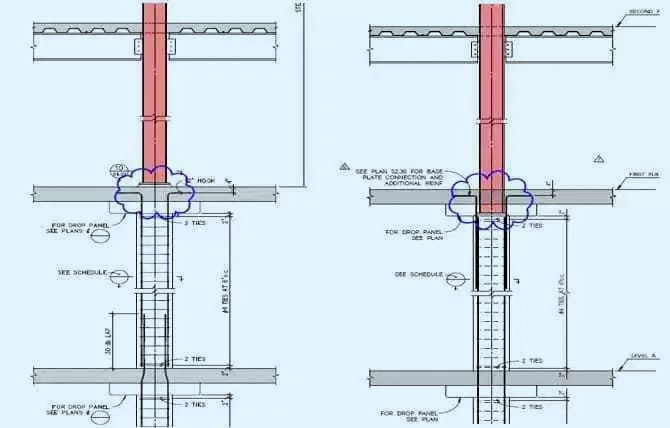
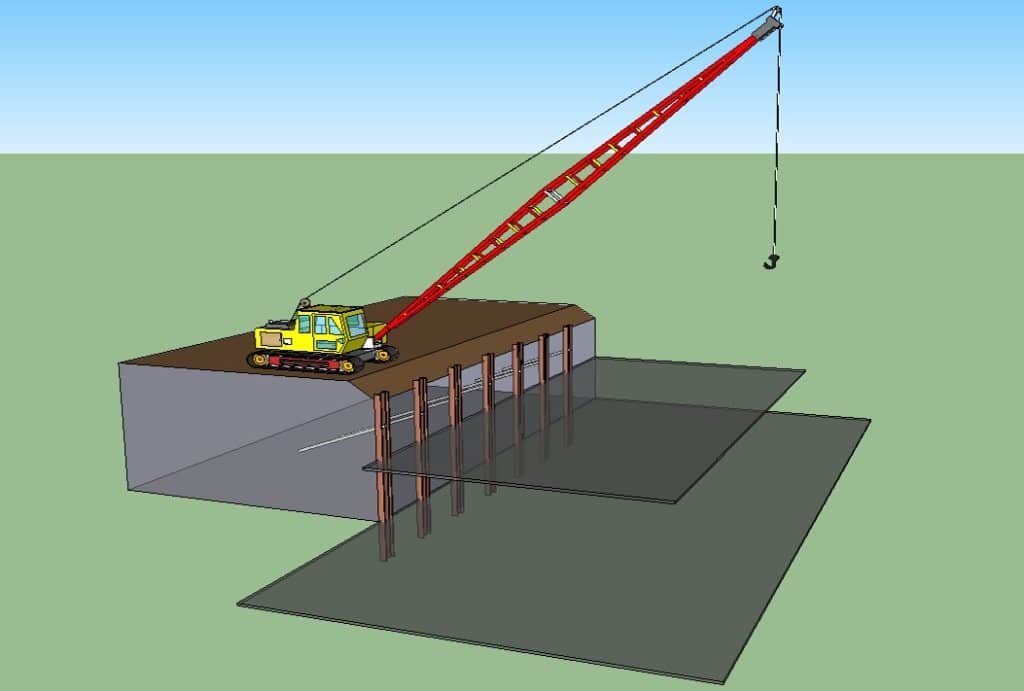
What Does This Mean for Site Logistics?
- In the original plan, the crane for the steel erection sits on the podium deck.
- In the proposed plan, the podium deck is not there and it isn't feasible to put the crane in the hole on the lower deck (no ramp).
- The crane can be placed outside the footprint of the new building, but this is in a public street.
- The team needs to negotiate with the local municipality to close the public street for the crane.
- The structural engineer needs to run calculations to make sure the tie backs for the exacavation will hold under the weight of the crane.
Coordinating the Smaller Details.
- In the initial planning, it was overlooked that some of the steel columns don't land on concrete columns.
- The smaller tube steel sections land on base plates on the podium deck because there are open drive aisles below them.
- In this case, the steel needed to extend all the way to the lower level deck to erect the building,
- The tube steel contains a base plate at the elevation of the future podium deck (in the middle of their height).
- Once the podium deck was placed, the lower portion of the tube steel was cut off and the underside of the deck was patched.
There was also an issue with the erection sequencing since the steel couldn't be erected to the third level until the decking was placed on the 2nd floor. This was due to height restrictions and safety for the erection crew. This would not have been the case for a building of this size if the podium had been in place.

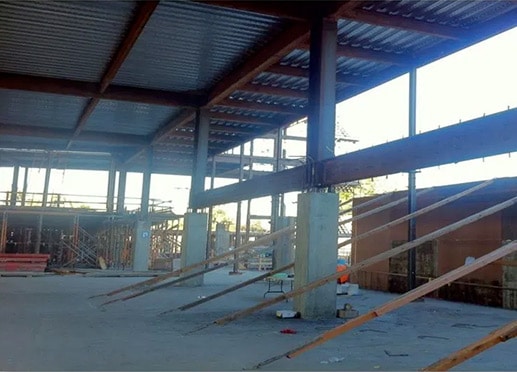
Conclusion: Yes it is Possible!
- The structural engineer spent almost $100,000 revising the steel, concrete and rebar details.
- The structural steel scope increased due to the longer columns and tube steel sections.
- The concrete and rebar scopes changed due to the alternate details and sequencing.
- Placement of the podium deck rebar and concrete was less efficient as it was built under the steel building.
- The tenant improvement started 10 weeks earlier than originally planned.
- This resulted in a net $500K savings to the project due to reduced general conditions.
- The building opened for its intended use 10 weeks earlier than planned and this was known a full 18 months prior to completion.
Outcome: This was done with no contractual change orders. All of the affected parties were design and trade partners. They were reimbursed their costs for the additional work and shared in the overall savings with a shared savings bonus. The owner shared in the savings as well, didn't need to negotiate for the savings through the change order process (taking cents on the dollar), and opened their building 10 weeks earlier.